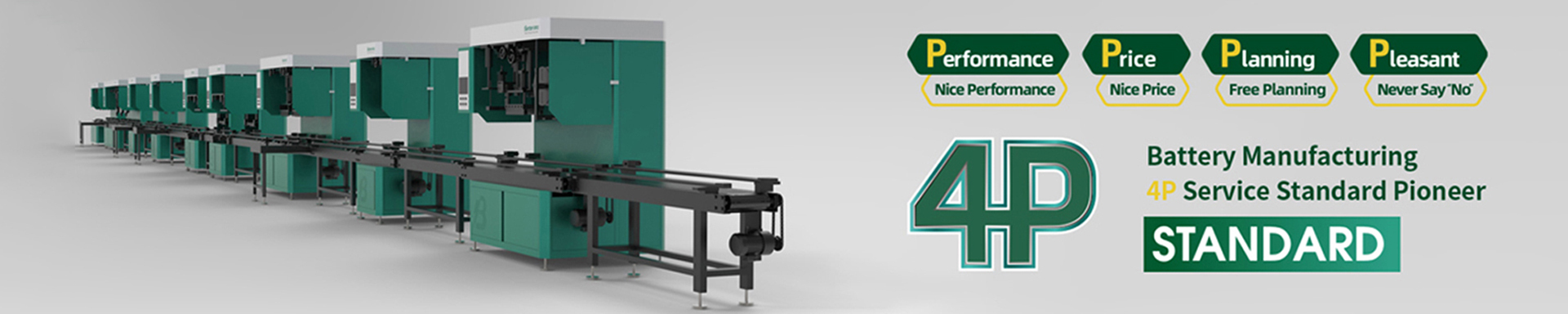
Which part of lead-acid battery production most affects the battery service life?
2023-04-03 18:00Lead-acid battery is a common storage battery, widely used in automobile, motorcycle, UPS power supply and other fields. In the production process of lead-acid battery, there are many links that will affect the service life of the battery, such as the production process of positive plate and negative plate, electrolyte formula, battery molding, capacity detection, etc. But which factor affects battery life the most? This article will analyze from several aspects.
1. Positive plate and negative plate production process
Positive plate and negative plate are the core components of lead-acid battery, and the manufacturing process has an important impact on the battery's service life. It includes lead plate preparation, active material mixing, lead paste preparation, spray molding and other links, among which the most influential is the preparation of active material.
The production of active materials requires strict process control. If the process is improper, it will lead to uneven thickness and distribution of active material particles, which will affect the capacity and life of the battery. In addition, the manufacturing process of positive plate and negative plate also needs to consider the purity and ratio of materials, which will directly affect the life of the battery.
2. Electrolyte formulation
Electrolyte is an important component of lead-acid battery, which contains sulfuric acid, water and additives. The formula of electrolyte has an important effect on the capacity, life and performance of battery. If the content of the electrolyte is not appropriate, it will lead to the reduction of battery capacity, increase in self-discharge, internal resistance and other problems.
The formula of the electrolyte needs to be determined through rigorous experiments and tests, taking into account the concentration and proportion of the components in the electrolyte, as well as the type and amount of additives and other factors. The electrolyte formulation should match the design and process of the battery to achieve the best battery performance.
3. Battery forming
Battery forming refers to the combination of positive plate, negative plate, separator and electrolyte components together to form a complete battery. The battery forming process will affect the internal structure and performance of the battery, thus affecting the service life of the battery.
Battery forming requires strict process control to ensure the fit and tightness of each component, while also taking into account factors such as battery tightness and stability. If the battery is not formed properly, it will lead to the internal structure of the battery is unstable, electrolyte leakage and other problems, thus affecting the service life of the battery.
Capacity detection is an important step in the production of lead-acid battery and one of the key factors affecting the battery life. Capacity test refers to the charge and discharge test of the battery to test whether the capacity of the battery meets the specified requirements.
If the capacity detection is not strict, the battery capacity will be insufficient or beyond the specified range, which will affect the service life of the battery. In addition, the capacity measurement also needs to take into account the influence of temperature, current and other factors on the battery capacity to ensure the accuracy and reliability of the test results.
In summary, in the production process of lead-acid batteries, the manufacturing process of positive and negative plates, electrolyte formula, battery molding and capacity detection will affect the service life of batteries. Among them, the production process of positive plate and negative plate and the electrolyte formula have significant influence on the battery, so special attention should be paid to it. At the same time, battery forming and capacity detection are also the key links affecting battery life, need strict control and management. Only in all links have been fully paid attention to and optimization, in order to produce stable quality, excellent performance of lead-acid batteries to meet the needs of different fields.