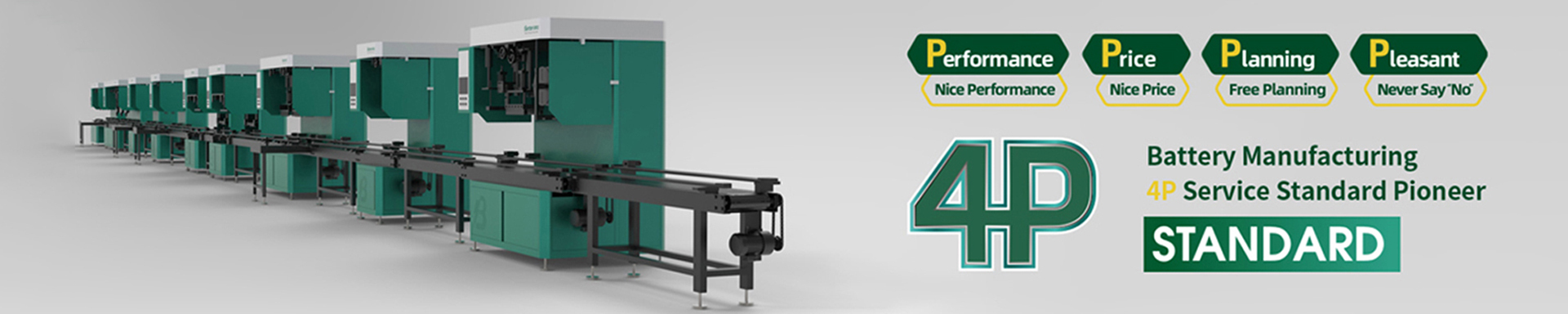
What Are the Basics of Lead Acid Battery?
2025-02-22 18:00Lead-acid batteries have been the go-to solution for many energy storage needs for more than a century, thanks to their reliability, cost-effectiveness, and long-lasting performance. These batteries are widely used in applications such as vehicles, backup power systems, and industrial energy storage. To understand the fundamentals of lead-acid batteries, it’s important to look into their production process, which involves several key components and machinery. In this article, we will explore the basics of lead acid battery technology, with a focus on the critical battery manufacturing machine, battery assembly line, battery production machine, and lead acid battery assembly line.
1. Understanding the Lead Acid Battery
A lead-acid battery consists of several essential parts: positive plates made of lead dioxide, negative plates made of spongy lead, a sulfuric acid electrolyte, separators to prevent short circuits, and a durable case to contain all the components. When the battery discharges, the lead plates react with the sulfuric acid to form lead sulfate, releasing electrical energy. During charging, the lead sulfate is converted back into lead and lead dioxide, allowing the battery to store energy for future use.
Lead-acid batteries are popular due to their ability to provide high surge currents, long cycle life, and relatively low cost. They are commonly used in automotive applications, uninterruptible power supplies (UPS), and industrial equipment, among other uses. While newer battery technologies like lithium-ion are gaining popularity, lead-acid batteries remain a staple in the energy storage industry due to their robustness and reliability.
2. Battery Manufacturing Machine: Essential for Efficiency
The production of lead-acid batteries requires specialized battery manufacturing machines designed to handle the various processes involved in battery creation. These machines are responsible for shaping the plates, mixing the electrolyte, and performing the chemical reactions required for energy storage.
For example:
Lead Oxide Machines: These machines produce the lead oxide used in the formation of the positive and negative plates. The lead oxide is mixed into a paste, which is then applied to the plates to create the required active material.
Plate Pressing and Rolling Machines: These machines form the electrode plates, ensuring they meet the exact size and consistency needed for the battery.
Electrolyte Mixing Machines: These machines mix the sulfuric acid and water in the correct proportions to create the electrolyte solution that will be used in the battery.
Battery manufacturing machines are designed to handle high volumes, ensuring that production lines are fast, consistent, and reliable. Automation in this stage increases efficiency and reduces human error, making it easier to produce large quantities of batteries with the required specifications.
3. Battery Assembly Line: Streamlining the Production Process
A battery assembly line is the backbone of the entire battery manufacturing process. It brings together various machines, workers, and components to assemble the individual parts into a fully functional battery. The assembly line ensures that each step of the production process is carried out systematically, allowing for quick, efficient production.
The battery assembly line typically involves the following stages:
Plate Assembly: The positive and negative plates are carefully aligned and stacked in a specific order, ensuring that they don’t touch each other to prevent short circuits. Separators are inserted between the plates to maintain proper spacing.
Electrolyte Filling: Once the plates are assembled, the electrolyte solution is added to the battery case, completing the internal structure.
Sealing and Testing: After the assembly is complete, the battery is sealed, and extensive testing is conducted to ensure that it meets performance standards. This includes testing for voltage, current, capacity, and overall battery health.
An efficient battery assembly line ensures that each battery is assembled with precision, improving both the quality and quantity of output. This results in lower production costs and ensures that batteries meet high-performance standards.
4. Battery Production Machine: Ensuring Consistency and Precision
A battery production machine is a type of automated equipment used to carry out specific tasks in the manufacturing process of lead-acid batteries. These machines are integral to ensuring that every component of the battery is produced with precision and consistency.
Some examples of battery production machines include:
Plate Formation Machines: These machines are used to chemically treat the lead plates to form the lead dioxide on the positive plates and spongy lead on the negative plates. The formation process involves charging the plates, which causes a chemical reaction between the lead oxide and sulfuric acid to create the desired active material.
Welding Machines: After the plates are formed, welding machines are used to connect the plates and other components together, ensuring a strong and secure electrical connection within the battery.
Testing and Inspection Machines: These machines test the performance of each battery, ensuring that it meets all necessary standards for capacity, voltage, and functionality before it is sent to market.
The use of specialized battery production machines reduces labor costs and human error, increases the speed of production, and ensures the final product’s consistency and reliability.
5. Lead Acid Battery Assembly Line: A Specialized Production System
The lead acid battery assembly line is specifically designed to handle the unique requirements of lead-acid battery production. These lines are equipped with a range of specialized machines and processes to ensure the successful assembly of each battery while maintaining high standards of quality.
The lead acid battery assembly line typically includes:
Material Handling Systems: These systems are responsible for moving raw materials, such as lead plates, electrolyte, and separators, through the various stages of the assembly process.
Automated Plate Handling and Assembly: The plates are automatically stacked, aligned, and positioned to ensure proper assembly without human intervention. This helps avoid errors and reduces labor costs.
Automated Sealing and Packaging: Once the battery is assembled, it undergoes an automated sealing process to ensure it remains secure during transportation and use. Packaging systems also help to efficiently prepare the batteries for shipping.
A properly designed lead acid battery assembly line can significantly increase the speed and scale of production while maintaining the quality and safety standards required for lead-acid batteries.
Conclusion
Lead-acid batteries are built from several key components, and the manufacturing process requires specialized equipment to ensure that each part is produced with precision. The use of battery manufacturing machines, battery assembly lines, and battery production machines streamlines the entire process, making it faster, more efficient, and more consistent. The lead acid battery assembly line is designed specifically to handle the production of lead-acid batteries, from assembling plates to filling the electrolyte and testing the final product.
By automating these processes, manufacturers are able to meet the growing demand for lead-acid batteries in various industries, ensuring that the batteries perform reliably and efficiently for years. Whether in automotive applications, industrial systems, or backup power solutions, understanding the basics of lead acid battery production is essential for anyone involved in energy storage technology.