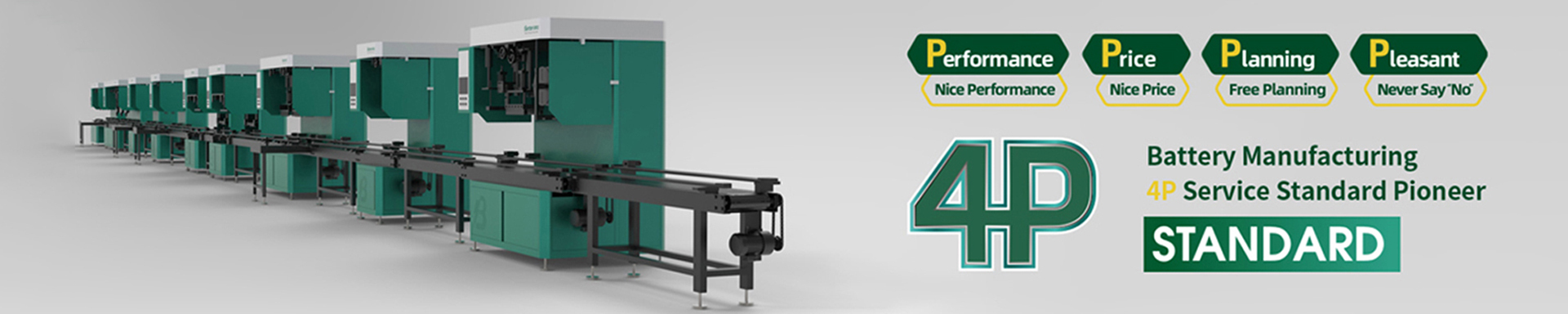
What Is the Structure of a Sealed Lead-Acid Battery?
2025-03-20 18:00Sealed lead-acid (SLA) batteries are widely used in various applications, including backup power systems, electric vehicles, and industrial machinery. These batteries are valued for their reliability, low maintenance, and cost-effectiveness. Understanding their structure is crucial for manufacturers and businesses investing in lead acid battery making machines and battery assembly line manufacturers to optimize production efficiency.
For those setting up a battery production facility, selecting the right battery making machine is essential. Additionally, the battery heat sealing machine plays a vital role in ensuring durability and leak-proof construction. This article explores the internal structure of sealed lead-acid batteries and highlights key machinery used in their manufacturing process.
1. The Structure of a Sealed Lead-Acid Battery
A sealed lead-acid battery consists of several essential components, each contributing to its functionality and efficiency.
1.1 Battery Case and Cover
The outer casing of an SLA battery is made from durable, acid-resistant plastic to protect internal components. During manufacturing, a battery heat sealing machine is used to securely seal the case, preventing electrolyte leaks and ensuring longevity.
1.2 Positive and Negative Plates
Inside the battery, multiple lead-based plates are arranged in alternating layers:
Positive Plates: Made of lead dioxide (PbO₂), these plates store and release energy.
Negative Plates: Composed of pure lead (Pb), these plates complete the electrochemical reaction.
High-quality lead acid battery making machines are essential in producing uniform, high-performance plates for energy-efficient batteries.
1.3 Separators
Thin insulating separators made from porous materials are placed between positive and negative plates. These separators allow ionic flow while preventing direct contact between plates, reducing the risk of short circuits.
1.4 Electrolyte (Absorbed or Gelled)
Unlike traditional flooded lead-acid batteries, SLA batteries contain absorbed or gelled electrolytes. The electrolyte enables the chemical reaction between the plates to generate electricity. The sealing process, done with a battery heat sealing machine, ensures that no electrolyte leaks occur.
1.5 Terminal Posts
Battery terminals serve as the connection points for external devices. They are designed to provide efficient electrical conductivity and ensure stable energy output.
1.6 Safety Valves (for VRLA Batteries)
Sealed lead-acid batteries use valve-regulated lead-acid (VRLA) technology, incorporating pressure-sensitive safety valves to release excess gas and prevent overpressure.
By utilizing an efficient automatic battery assembly line, manufacturers can ensure precise placement of these components, improving battery quality and performance.
2. Manufacturing a Sealed Lead-Acid Battery
Producing high-quality SLA batteries requires advanced machinery, including lead acid battery making machines, automated assembly lines, and battery heat sealing machines. The following steps outline the manufacturing process:
2.1 Grid Casting
The production process begins with casting lead grids, which act as the structural framework for battery plates. Automated battery making machines ensure uniformity in grid thickness and design.
2.2 Paste Application & Curing
A lead oxide paste is applied to the grids to create active material layers. The plates are then dried and cured to enhance strength and conductivity.
2.3 Battery Assembly
During this stage, the positive and negative plates are stacked together with separators and inserted into the battery case. Battery assembly line manufacturers provide high-speed automation solutions to streamline this process.
2.4 Battery Heat Sealing
A battery heat sealing machine is used to securely bond the battery cover to the case, ensuring an airtight seal to prevent leaks. The battery heat sealing machine price varies depending on automation level, sealing technology, and production capacity.
2.5 Electrolyte Filling & Formation
After sealing, the battery is filled with an absorbed or gel electrolyte and undergoes an initial charging cycle to activate its chemical reactions.
2.6 Quality Testing & Final Packaging
Each battery is tested for voltage, capacity, and durability before packaging. An automated battery assembly line ensures consistent quality control and efficient handling.
3. Factors Influencing Battery Making Machine Price
Investing in high-quality lead acid battery making machines is crucial for manufacturers looking to optimize production. The battery making machine price depends on:
Automation Level: Fully automated systems cost more but provide long-term efficiency and reduced labor costs.
Production Capacity: High-speed machines designed for mass production have a higher price.
Technology & Features: Machines with AI-driven controls and precision engineering command a premium price.
Durability & Maintenance: Investing in robust machinery reduces long-term maintenance costs.
When choosing battery assembly line manufacturers, it is essential to consider their technology offerings and support services.
4. Why Invest in an Efficient Automatic Battery Assembly Line?
A modern battery assembly line enhances manufacturing precision and reduces waste. Key benefits include:
Higher Production Efficiency: Automation speeds up assembly and minimizes human error.
Cost Savings: Reduces labor and material waste, optimizing operational expenses.
Consistent Quality: Ensures uniformity in battery assembly and sealing.
Scalability: Allows for seamless expansion as demand increases.
5. Future Trends in Lead-Acid Battery Manufacturing
With advancements in battery production technology, manufacturers are increasingly adopting:
AI-Integrated Battery Assembly Lines: Smart automation systems for real-time monitoring and process optimization.
Eco-Friendly Battery Manufacturing: Innovations in lead recycling and energy-efficient production methods.
Advanced Sealing Techniques: Enhanced battery heat sealing machines that provide stronger and more reliable seals.
Conclusion
The structure of a sealed lead-acid battery consists of essential components like positive and negative plates, separators, electrolyte, and a securely sealed case. The manufacturing process requires high-quality lead acid battery making machines and an efficient automatic battery assembly line to ensure precision and durability.
Investing in the right battery making machine and battery heat sealing machine is crucial for optimizing production quality and efficiency. While the battery making machine price varies based on automation and capacity, choosing a reliable battery assembly line manufacturer can lead to long-term cost savings and improved product performance.
For manufacturers looking to stay competitive, adopting advanced lead acid battery making machines and automated production lines is the key to success in the energy storage industry.