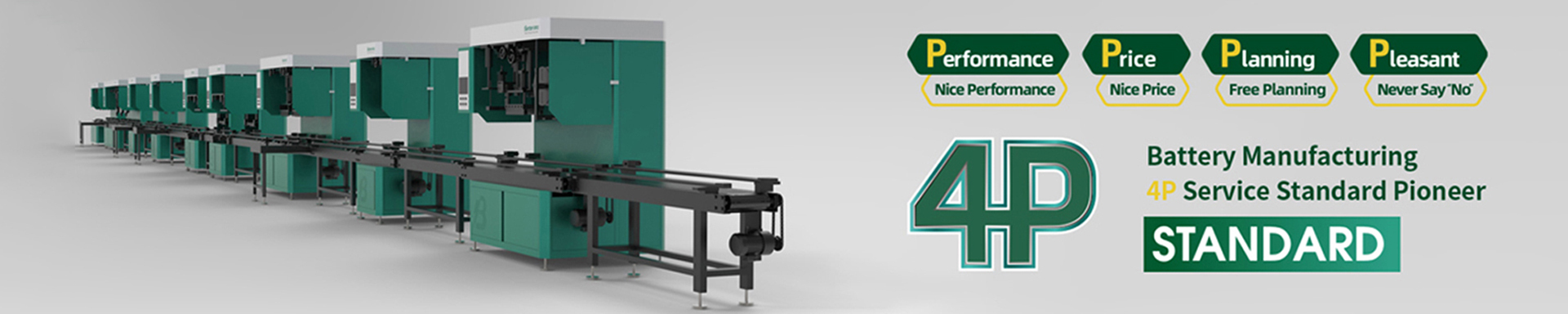
Production Process of Lithium Battery Pack Cells
2025-02-11 18:00The packaging of lithium-ion batteries is divided into two categories: metal shell batteries and pouch batteries. The production process of lithium battery pack cells is divided into three major stages: electrode production, cell production, and battery assembly.
What are the main production processes of the lithium battery pack?
Mixing (positive and negative active materials + conductive agent + binder + dispersant) - coating - rolling - slitting – electrode tab welding - winding (or gasket) - pasting adhesive tape – loading into the battery shell —welding—sealing—formation, etc.; the battery production process of the entire industry is similar, the main difference is the different equipment or battery products, for example, pouch lithium batteries include general stacking, cylindrical winding, square winding and stacking coexist. This causes the battery cells to be different during the winding process; the most important core technologies are mixing and coating, as well as the final formation.
The production process of lithium battery packs is relatively complex. The main production process mainly covers the stirring and coating stage of electrode production, the winding and electrolyte injection stage of battery cell synthesis, and the packaging and testing stage of formation. The value volume accounts for about (35~40 %):(30~35)%:(30~35)%. The differences mainly come from different equipment suppliers, differences in the import/domestic ratio, etc. The processes are basically the same, and the value share has deviations but is generally in line with this ratio.
The lithium battery pack production equipment used in the first stage mainly includes a vacuum mixer, coating machine, roller press, etc.; the middle process mainly includes die cutting machine, winding machine, laminating machine, electrolyte injection machine, etc.; the post-process mainly includes forming machines, grading and testing equipment, warehousing and logistics automation, etc. In addition, the production of battery packs also requires Pack automation equipment.
The middle process is mainly to form the battery, including electrode producing, electrode sheet winding, die cutting, cell winding forming lamination forming, etc., which is a fierce competition area for current domestic equipment manufacturers.
The post-production process of lithium battery packs mainly consists of four steps: grading, formation, testing, and packaging & warehousing. As the most important links in the post process, formation, and capacity grading are used to activate and test the formed batteries. Since the battery charge and discharge test cycle are long, the equipment has the highest value. The main function of the formation process is to charge and activate the battery cells after electrolyte injection and packaging, while the capacity grading process is to test the battery capacity and other electrical performance parameters after the battery is activated and to grade them.
The production process of pouch lithium battery pack:
The pouch lithium batteries use hot packaging (because they use aluminum-plastic packaging film), while metal shell batteries generally use welding (laser welding).
First step: Electrode material preparing
Mixing, stirring, and dispersing the electrode active materials, conductive agents, binders, solvents, etc., and ultimately producing a slurry that meets the coating requirements.
Second step: Coating
Uniformly apply the fluid slurry onto the surface of the current collector (aluminum foil or copper foil), followed by drying solvents to form a film and produce battery electrodes.
Third step: Electrode sheets punching
Punch-cutting the electrode sheet into specified dimensions and shapes.
Fourth step: Stacking
Stacking positive and negative electrode sheets along with separators in alternating layers, and stick tape to complete the electrode assembly.
Fifth step: Assemble the pouch battery
Place the electrode produced in the previous step into the punch-formed aluminum-plastic film, and complete the top seal, side seal, etc. (leave a hole for electrolyte injection), to form a pouch battery without electrolyte injection;
Sixth step: Electrolyte injection
Inject specified liquid electrolytes into the battery through the injection port.
Seventh step: Battery sealing
Extract the gas in the battery and complete sealing in a vacuum environment.
Advantages of pouch lithium battery:
1. Good safety performance. The pouch lithium battery pack is structurally packaged with aluminum-plastic film. In the event of a safety hazard, the pouch battery will only bulge and crack at most, and will not explode like steel-shell aluminum-shell batteries.
2. Lightweight. Pouch lithium batteries are 40% lighter than steel-shell lithium batteries of the same capacity and 20% lighter than aluminum-shell batteries.
3. Large capacity. The capacity of pouch lithium battery packs is 10-15% higher than that of steel-shell batteries of the same specifications and size, and 5-10% higher than that of aluminum-shell batteries.
4. Small internal resistance. The internal resistance of pouch batteries is smaller than that of lithium batteries. At present, the internal resistance of domestic pouch battery cells can be as low as 35mΩ, which greatly reduces the battery's self-consumption.
Flexible design. The shape of the pouch lithium battery can be customized according to customer needs to develop new battery cell models.