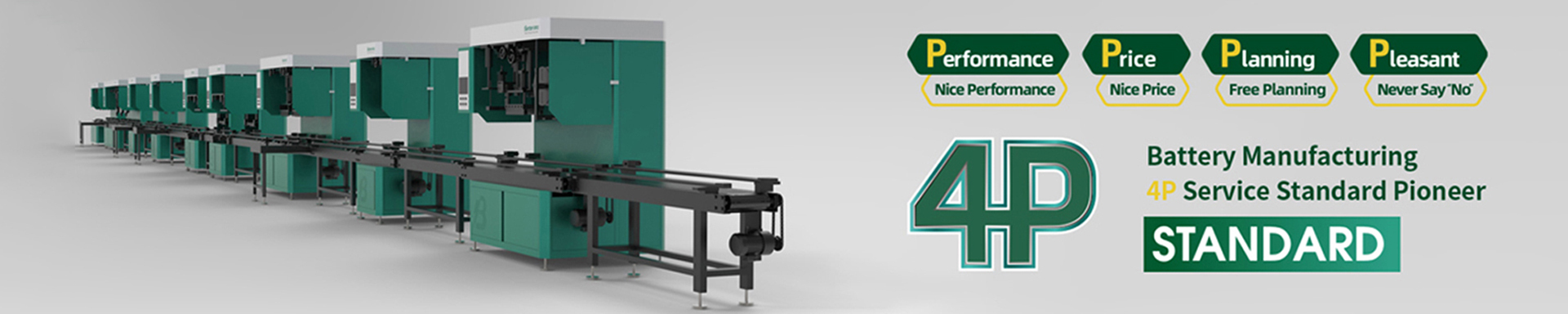
High-Efficiency Industrial Dimensional Testing Machine: A Dual Assurance of Precision and Efficiency
2024-10-11 18:00Table of Contents
Overview of the High-Efficiency Industrial Dimensional Testing Machine
Product Features and Technical Advantages
2.1. Functional Features
2.2. Technical Specifications
Standard Operating Procedures and Maintenance Guidelines
Extensive Applications and Solutions
4.1. Consumer Electronics Manufacturing
4.2. New Energy Battery Production
4.3. Aerospace Components Manufacturing
4.4. Precision Instruments Manufacturing
Case Studies
5.1. Case 1: Large-Scale Electronics Manufacturer
5.2. Case 2: Aerospace Enterprise
Future Trends and Technological Development
Frequently Asked Questions (FAQ)
Conclusion
1. Overview of the High-Efficiency Industrial Dimensional Testing Machine
In modern industrial production, precision and efficiency are the core requirements for ensuring product quality and productivity. To meet these demands, enterprises rely on highly efficient, accurate testing equipment. The high-efficiency industrial dimensional testing machine is designed for various production lines, capable of rapidly and precisely measuring product dimensions to ensure compliance with strict design standards. This article will explore the key features, technical parameters, and its broad applications in different industrial sectors.
2. Product Features and Technical Advantages
2.1. Functional Features
High-Precision Measurement: The machine employs advanced optical measurement systems and high-sensitivity sensors, allowing precision measurements at the micron level. Its design emphasizes stability, ensuring that measurement accuracy is maintained even in high-intensity production environments.
Fast Detection Speed: With a detection rate of up to 1500 pieces per hour, the machine enables high-speed continuous testing on large-scale production lines, avoiding production bottlenecks caused by inspection delays.
Automation and Intelligence: The equipment features fully automated operations, from material feeding, testing, data analysis, to sorting, all controlled by the system. Additionally, its intelligent data processing system analyzes results in real-time and categorizes products based on preset standards.
Compatibility with Multiple Specifications: The machine supports the detection of products with various specifications. Users can easily adjust measurement parameters according to production needs, ensuring compatibility with different product batches.
Easy Integration and Maintenance: Its streamlined design ensures easy integration into existing production lines. Equipped with self-diagnosis and remote maintenance capabilities, the machine allows real-time monitoring and maintenance via the internet, reducing downtime.
2.2. Technical Specifications
Parameter | Specification |
Transmission Size (Tj/mm) | L: 40-120, W: 35-90, T: 3-8 |
Measurement Accuracy | ±0.02 mm |
Detection Speed | 1500 PCS/H |
Operating Pressure | 0.5 MPa |
Power Consumption | 2 KW |
Operating Temperature | 0~50℃, Humidity: 30%-95% |
Power Requirements | 220V 50Hz |
Equipment Dimensions | 1400×1290×1900 mm |
3. Standard Operating Procedures and Maintenance Guidelines
To ensure optimal performance, the following standard operating procedures and maintenance guidelines should be followed:
Product Feeding: Load the products to be tested into the machine using an automated feeding device. The equipment will begin the testing process automatically.
High-Precision Testing: The machine’s optical sensors and measurement system will precisely measure the products, recording dimensional data in real-time.
Data Analysis and Sorting: The system automatically analyzes the data and sorts defective products to ensure that only compliant items proceed to the next production stage.
Routine Maintenance: Regular maintenance includes cleaning the sensors, checking system calibration, and updating the machine's software. The self-diagnosis feature helps detect potential issues early, ensuring stable operation.
4. Extensive Applications and Solutions
4.1. Consumer Electronics Manufacturing
In consumer electronics manufacturing, the dimensional accuracy of components is critical for product performance. The high-efficiency industrial dimensional testing machine can quickly measure the dimensions of various electronic components, ensuring each part meets the strict design specifications.
4.2. New Energy Battery Production
The production of new energy batteries demands high dimensional precision. The machine provides efficient quality testing solutions, ensuring that every battery produced meets design requirements with high accuracy.
4.3. Aerospace Components Manufacturing
In aerospace component manufacturing, dimensional precision directly affects aircraft safety. The machine provides reliable dimensional testing throughout the production process, ensuring that every component meets industry standards, thereby enhancing product safety.
4.4. Precision Instruments Manufacturing
In the production of precision instruments, dimensional errors can have a significant impact on performance. The high-efficiency industrial dimensional testing machine offers high-precision detection for this sector, ensuring product quality, stability, and reliability.
5. Case Studies
5.1. Case 1: Large-Scale Electronics Manufacturer
A leading electronics manufacturer introduced the high-efficiency industrial dimensional testing machine into its new smartphone production line. The equipment's efficient testing capability significantly boosted production line efficiency and reduced defect rates, giving the company a competitive edge in the market.
5.2. Case 2: Aerospace Enterprise
An aerospace company applied the machine in its new unmanned aerial vehicle (UAV) project. The machine’s high-precision measurement ensured the dimensional accuracy of critical components, improving overall stability and reliability of the UAV.
6. Future Trends and Technological Development
As manufacturing moves toward greater automation and intelligence, the high-efficiency industrial dimensional testing machine will continue to evolve. Future upgrades will likely include more advanced sensor technology, AI-driven data analysis, and a more user-friendly interface. Additionally, with the growth of the Industrial Internet of Things (IIoT), the machine will further integrate with other production equipment, facilitating comprehensive intelligent production line management.
7. Frequently Asked Questions (FAQ)
Which industries is this equipment suitable for?
The high-efficiency industrial dimensional testing machine is ideal for various industries, including consumer electronics, new energy batteries, aerospace components, and precision instrument manufacturing.
What is the measurement accuracy of the machine?
The measurement accuracy is ±0.02 mm, meeting the high precision requirements of modern manufacturing.
How should the equipment be maintained daily?
Routine maintenance includes cleaning the sensors, checking calibration, and updating software. The self-diagnosis feature helps detect issues early.
Can the machine adapt to different product specifications?
Yes, the machine supports multi-specification product detection. Users can adjust testing parameters as needed.
Does the machine support remote monitoring and maintenance?
Yes, the machine supports remote monitoring and maintenance, allowing users to view equipment status in real-time, reducing maintenance costs and downtime.
8. Conclusion
With its superior precision, fast detection speed, and highly automated operations, the high-efficiency industrial dimensional testing machine has become an indispensable quality control tool in modern manufacturing. As technology advances, this machine will see broader applications and provide strong support for the intelligent and precise development of the manufacturing industry.