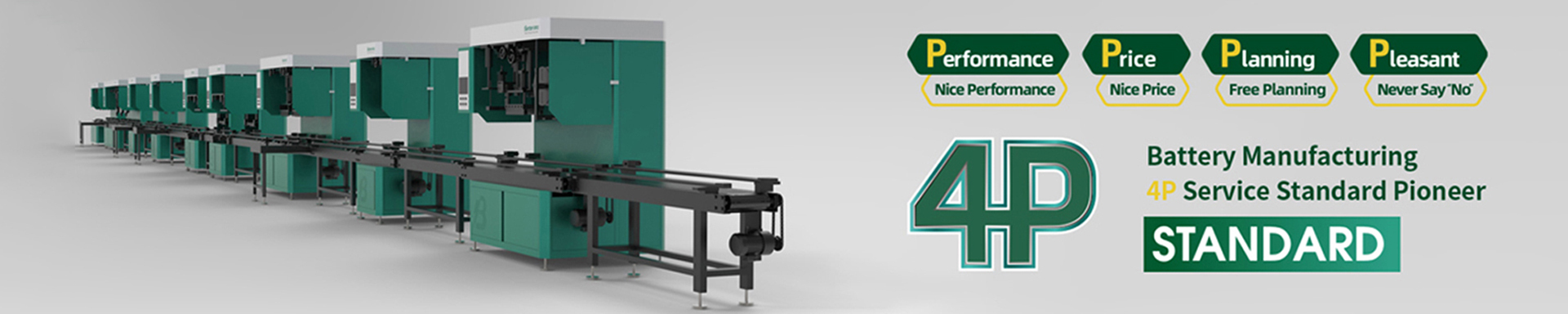
Enhancing Production Line Automation: Integration and Optimization of the Protective Plate Adhesive Bending Machine
2024-10-25 18:00Introduction
In modern manufacturing, improving automation is essential for increasing production efficiency and product quality. The protective plate adhesive bending machine, as a highly efficient automated device, plays a vital role in realizing the automation and intelligence of production lines. This article explores how to integrate the protective plate adhesive bending machine into existing production lines and optimize its operation to further enhance the overall performance of the production line.
I. Challenges in Integrating Automated Production Lines
1. Complexity of Multi-Equipment Coordination
Automated production lines typically consist of various devices, including feeding equipment, processing machines, inspection devices, and discharge units. Ensuring the smooth coordination of these devices requires seamless communication and action synchronization between them. When integrating the protective plate adhesive bending machine, it is essential to achieve smooth connectivity with other devices to maintain the stability and efficiency of the production line.
2. Data Communication and System Compatibility
Modern automated production lines increasingly rely on data-driven decision support systems like Manufacturing Execution Systems (MES) and Enterprise Resource Planning (ERP) systems. During the integration of the protective plate adhesive bending machine, ensuring compatibility and data exchange with these systems is crucial. This requires the equipment to have open interfaces and flexible communication protocols, allowing real-time transmission of production data and receiving system instructions.
3. Ease of Maintenance and Fault Handling
As automation levels increase, maintaining and troubleshooting production lines becomes more complex. Equipment integration must consider production efficiency while ensuring rapid fault detection and resolution to minimize downtime. The intelligent monitoring and predictive maintenance features of the protective plate adhesive bending machine offer essential support in this regard.
II. Advantages of Integrating the Protective Plate Adhesive Bending Machine
1. Flexible Interface Design
The protective plate adhesive bending machine offers various interface designs, enabling seamless connection and collaboration with other devices. It includes standard Ethernet interfaces, RS-232/RS-485 ports, and optional wireless communication modules, ensuring smooth integration within diverse industrial network environments. Through these interfaces, the equipment can exchange real-time data with other devices on the production line, achieving precise synchronization.
2. Highly Customizable Operating System
The operating system of the machine is highly customizable and can be adjusted according to the specific needs of the production line. It supports multiple programming languages and protocols, allowing engineers to create custom programming as needed. This level of customization ensures the equipment can meet specific production line requirements, whether it's synchronizing production rhythms or planning complex bending paths.
3. Intelligent Monitoring and Maintenance
The machine incorporates an advanced intelligent monitoring system that tracks real-time operational status, processing accuracy, and workload. When anomalies are detected, the system can automatically adjust or send alerts to prevent failures. This intelligent monitoring and maintenance capability not only enhances operational stability but also significantly reduces downtime and maintenance costs.
4. Quick Switching and Multi-Task Processing Capability
The machine is capable of fast switching and multi-task processing, allowing it to handle different product tasks within a short time. This is particularly important for companies that frequently switch product types on the production line. The protective plate adhesive bending machine can quickly adjust parameters and operations according to different protective plate requirements, reducing manual adjustments and enhancing production flexibility and adaptability.
III. Case Studies of Integration Optimization
1. Integration and Optimization in a Consumer Electronics Production Line
In a large consumer electronics manufacturer’s production line, the protective plate adhesive bending machine was integrated for producing smartphone battery protection plates. The seamless connection with feeding and inspection equipment significantly optimized the production process. The intelligent monitoring function not only improved production stability but also reduced defects through real-time adjustments.
Specific Parameters: After integration, the production capacity increased to 15,000 PCS/H, and the equipment yield remained above 98%.
Optimization Effect: The automation level of the production line was significantly enhanced, manual intervention reduced by 40%, and overall production efficiency improved by 25%.
2. Application in New Energy Battery Production Line
In the production of new energy batteries, processing the protective plate is a critical step. A new energy battery manufacturer integrated the protective plate adhesive bending machine into its fully automated production line. By connecting to the MES system, the machine could receive real-time production instructions and adjust processing parameters. This integration dramatically improved the responsiveness and flexibility of the production line.
Battery Protection Plate Size Range: L 40-120mm, W 35-90mm, T 3-10mm. The machine accurately handled various sizes of protective plates.
Performance Improvement After Integration: The overall efficiency of the production line improved by 30%, and the processing precision of the protective plates reached micron levels.
3. Intelligent Upgrades in a New Materials Production Line
In a production line of a new materials company, the protective plate adhesive bending machine was used to process high-strength, lightweight protective plates. The machine's flexibility and high precision made it ideal for the unique processing demands of new materials. Through integration with an Industrial Internet of Things (IIoT) platform, the machine enabled real-time data collection and remote monitoring, further enhancing the production line's intelligence.
Smart Data Integration: The machine uploaded production data to the IIoT platform in real-time, supporting management-level analysis and decision-making.
Remote Maintenance and Optimization: The intelligent maintenance module utilized big data analytics to enable predictive maintenance, reducing failure rates by 20% and maintenance costs by 15%.
IV. Recommendations for Optimizing Production Lines
1. Optimizing Equipment Layout and Process Design
When integrating the protective plate adhesive bending machine, it is essential to optimize the equipment layout and operation process according to the specific needs of the production line. A well-planned layout can reduce material transfer time and operation wait time, thus improving overall production efficiency.
2. Enhancing Data Analysis and Decision Support
Integrating the machine’s data with the production line’s management system enables transparency in the production process and data-driven decision support. It is recommended that companies use data analytics tools to monitor the performance indicators of the production line in real-time and make adjustments as needed.
3. Continuous Improvement and Upgrades
As technology evolves, the functions and performance of the protective plate adhesive bending machine will continue to improve. Companies should maintain close contact with equipment suppliers to stay updated on the latest upgrades and perform necessary software and hardware updates to maintain a leading position in production line automation.
V. Conclusion
As a key piece of equipment for improving production line automation, the protective plate adhesive bending machine offers flexible interface design, a highly customizable operating system, and intelligent monitoring and maintenance advantages. Through proper integration and optimization, the machine can significantly enhance the efficiency and product quality of production lines, providing strong support for enterprises aiming to achieve intelligent manufacturing. As automation and intelligence technologies continue to advance, the protective plate adhesive bending machine will play an increasingly important role in more industries, opening up new possibilities for production line optimization and upgrades.