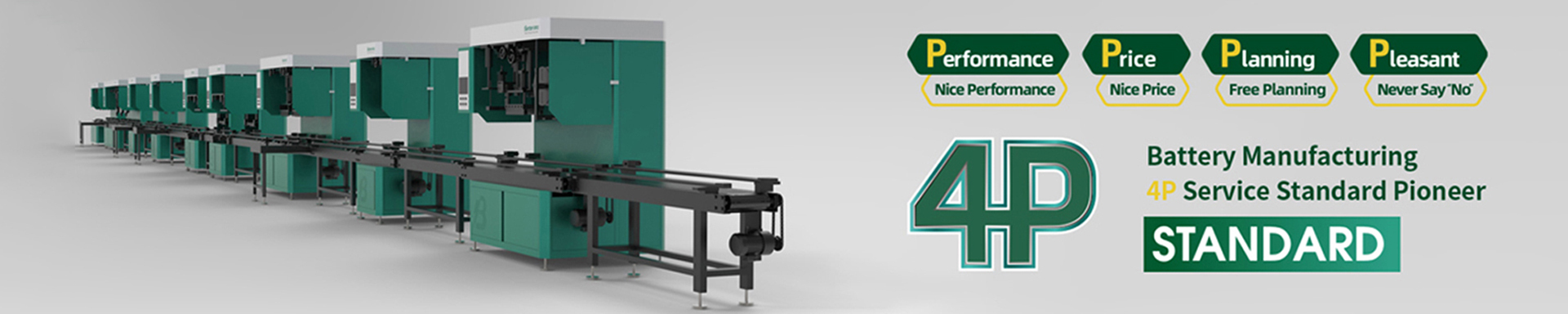
High-Efficiency Precision Dimensional Testing Machine: An Essential Tool for Quality Control in Manufacturing
2024-08-29 18:00Table of Contents
High-Efficiency Precision Dimensional Testing Machine: An Essential Tool for Quality Control in Manufacturing
Product Features and Technical Characteristics
Functional Features
Technical Specifications
Workflow and Operation Guide
Application Scenarios
Battery Manufacturing Industry
Electronic Components Production
Automotive Parts Manufacturing
Precision Instrument Manufacturing
Usage Scenarios and Examples
Example 1: A Lithium Battery Production Line
Example 2: A Precision Electronic Component Manufacturing Plant
Future Development and Outlook
Frequently Asked Questions (FAQ)
Conclusion
Product Overview
In modern manufacturing, quality control is a critical factor that determines product performance and market competitiveness. To ensure that product dimensions meet stringent design requirements, high-precision automated testing equipment has become an indispensable part of the production line. This article introduces a highly efficient precision dimensional testing machine widely used in industries such as battery manufacturing, electronic components, automotive parts, and more. The device, known for its exceptional accuracy, fast detection speed, and high level of automation, provides reliable quality assurance for various manufacturing sectors.
Product Features and Technical Characteristics
Functional Features
High Precision: The dimensional testing machine is equipped with advanced measurement sensors that can accurately measure the length, width, thickness, and other dimensional parameters of products with a precision of ±0.02mm. This ensures that products do not suffer from quality issues due to dimensional errors during production.
Fully Automated Operation: The device achieves fully automated measurement processes, from product loading, measurement, sorting, to data recording, all completed automatically by the equipment. This significantly improves production efficiency and reduces errors caused by manual intervention.
Data Management and Traceability: The equipment is equipped with an intelligent data management system that can record the measurement data of each product in real-time and generate detailed inspection reports, facilitating data analysis and traceability for quality management personnel.
Multi-Specification Adaptability: The device supports the measurement of products with different specifications. Users can quickly adjust equipment parameters according to production needs to accommodate the detection of products with various sizes and shapes.
Easy Maintenance: The dimensional testing machine is designed to be simple and easy to maintain. The equipment is equipped with self-diagnostic functions that can preemptively warn of potential issues, reducing downtime.
Technical Specifications
Transmission Size (Tj/mm): L:40-120 W:35-90 T:3-8
Length, Width, Thickness Measurement Accuracy: ±0.02mm
Thickness Testing Accuracy: Clamping with anti-vibration material, 300~1000gf, accuracy ±50gf
Clamping Pressure: 0.5MPa
Equipment Power: 2KW
Temperature and Humidity Range: 0~50℃, 30%~95% humidity
Power Requirements: 220V 50Hz
Speed (UPH): Approximately 1500PCS/H
Equipment Dimensions: Approximately 140012901900mm
Workflow and Operation Guide
The workflow of the dimensional testing machine is efficient and straightforward, suitable for various production lines. The following are the operational steps of this equipment:
Product Loading: Feed the products to be tested into the testing machine via a conveyor belt or automatic feeding device.
Precision Measurement: The device automatically measures the product's dimensional parameters, including length, width, and thickness, and records the measurement data.
Data Analysis: The system automatically analyzes the measurement data, compares it with the set standards, and determines whether the product meets the required specifications.
Automatic Sorting: For non-compliant products, the device will automatically sort them and move them to a designated area, ensuring that defective products do not enter the next production stage.
Terminal Transfer: Compliant products are transferred to the next process step through the terminal transfer device, completing the entire measurement process.
Application Scenarios
Battery Manufacturing Industry
In the battery manufacturing process, the dimensional precision of products directly affects battery performance and safety. The dimensional testing machine can quickly and accurately detect the external dimensions of batteries, ensuring that each battery complies with design specifications. This not only improves production efficiency but also reduces rework costs due to non-compliant dimensions.
Electronic Components Production
Electronic components demand extremely high precision. The dimensional testing machine can be used to check the casing dimensions of various electronic components, ensuring product reliability and stability. This plays a crucial role in improving the overall quality of electronic products.
Automotive Parts Manufacturing
The dimensional precision of automotive parts directly impacts vehicle performance and safety. The dimensional testing machine is widely used in automotive parts production lines to ensure that every part meets design standards, thereby improving the quality and reliability of the entire vehicle.
Precision Instrument Manufacturing
In the production of precision instruments, dimensional errors can significantly affect the functionality and performance of the equipment. The dimensional testing machine, through high-precision dimensional detection, ensures the accuracy of each component, thereby improving the overall performance and market competitiveness of the product.
Usage Scenarios and Examples
Example 1: A Lithium Battery Production Line
A well-known lithium battery manufacturer introduced the dimensional testing machine for quality inspection in their high-performance lithium battery production. The equipment can inspect thousands of batteries daily, significantly enhancing production efficiency while ensuring dimensional accuracy for each battery. The efficient operation of the equipment has further improved the company's product quality, gaining more customer trust in the market.
Example 2: A Precision Electronic Component Manufacturing Plant
In a precision electronic component manufacturing plant, the dimensional testing machine is used to detect the casing dimensions of chips. The high-precision measurement function of the device ensures seamless assembly of the chips during the manufacturing process, thereby enhancing the stability and reliability of the final product. This not only improves product quality but also increases customer satisfaction.
Future Development and Outlook
As Industry 4.0 advances, the application of automated testing equipment in manufacturing will become increasingly widespread. As an important quality control device, the dimensional testing machine will continue to develop towards higher precision, faster speed, and greater intelligence. By continuously optimizing measurement technology and data management systems, this equipment will be widely used in more industries, providing strong support for the intelligent upgrading of manufacturing.
Frequently Asked Questions (FAQ)
Which industries is the dimensional testing machine suitable for?
The dimensional testing machine is suitable for various industries, including battery manufacturing, electronic components production, automotive parts manufacturing, and precision instrument manufacturing.
What is the measurement accuracy of the device?
The device's measurement accuracy is ±0.02mm, meeting the needs of high-precision manufacturing industries.
How to adjust the equipment parameters to accommodate different product specifications?
The equipment supports multi-specification product detection. Users can quickly adjust the measurement parameters through the device's operation interface to meet the needs of different products.
Is the equipment maintenance-intensive?
The equipment requires relatively simple maintenance, mainly including regular cleaning, sensor calibration, and system checks. The built-in self-diagnostic function can help users preemptively detect potential issues.
Can the equipment be integrated with existing production lines?
Yes, the dimensional testing machine supports seamless integration with existing production lines and can be connected to other automated equipment through various interfaces.
Conclusion
The dimensional testing machine, with its high precision, automated operation, and ease of maintenance, has become an important device for improving quality control levels in modern manufacturing. As technology continues to progress and demand continues to grow, the application scope of dimensional testing machines will continue to expand, providing strong support for the intelligent development of the manufacturing industry.