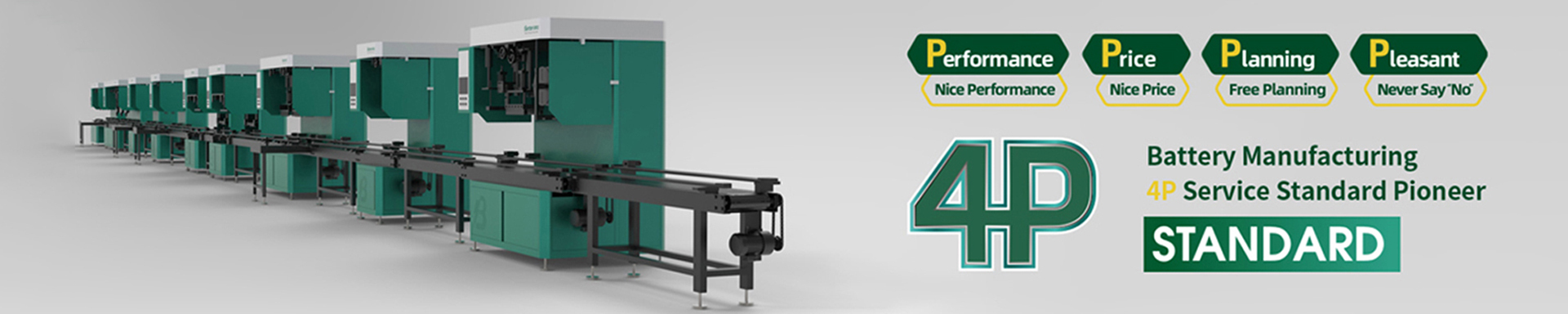
Automation Technology and Intelligent Control Systems of Glue Laminating Machine
2024-09-24 18:00Introduction
As the demand for efficient and precise production in the battery manufacturing industry continues to rise, automated and intelligent equipment have become crucial for enhancing production efficiency and product quality. The adhesive forming machine, with its advanced automation technology and intelligent control system, plays a vital role in the battery manufacturing process. This article provides an in-depth analysis of the automation principles, intelligent control systems, and the production advantages of Glue Laminating Machine.
Principles of Equipment Automation
The core advantage of the adhesive forming machine lies in its highly integrated automation control system. The device utilizes a PLC (Programmable Logic Controller) to achieve full-process automation control, covering all stages from feeding, adhesive application, to discharge. The PLC works in close coordination with sensors and actuators, enabling synchronized operation and precise control of all machine components.
Automation Workflow:
Automatic Feeding: Sensors detect the position of the electrode sheets and automatically feed them into the adhesive application area.
Automatic Adhesive Application: The PLC controller precisely controls the adhesive application process based on preset parameters, ensuring perfect adhesion of the adhesive film to the electrode sheets.
Automatic Waste Adhesive Removal: After the adhesive application, the machine automatically removes excess adhesive and collects it in a waste disposal unit.
Automatic Discharge: The completed electrode sheets are automatically transferred to the discharge area, ready for the next production stage.
This series of automated operations not only reduces manual intervention but also enhances production speed and output through efficient machine operation. The standardization and consistency of the automated process effectively reduce variability caused by manual operations, ensuring that each electrode meets high-quality standards.
Advantages of Intelligent Control
One of the key reasons the adhesive forming machine stands out in battery manufacturing is its intelligent control system. The intelligent control system includes real-time data monitoring, automatic parameter adjustment, and fault self-diagnosis, providing data-driven support for optimizing the production process.
Real-Time Data Monitoring: The machine is equipped with multiple high-precision sensors that monitor key parameters during the adhesive application process, such as adhesive film positioning and application force. Data is transmitted to the control system for analysis in real-time, and any detected deviations prompt the system to make immediate adjustments, ensuring precision in every operation.
Automatic Adjustment and Optimization: The intelligent control system not only operates based on preset parameters but also possesses self-learning and optimization capabilities. By continuously collecting and analyzing production data, the system can optimize parameters such as application speed and pressure, maintaining optimal machine performance under varying production conditions.
Fault Self-Diagnosis and Alarming: The built-in fault self-diagnosis module monitors the equipment's operational status in real-time. If abnormalities are detected, the system immediately triggers an alarm and halts operations to prevent equipment damage or production accidents. This design protects the equipment and ensures operator safety.
Technological Innovations and Future Development
With the advancement of Industry 4.0 and smart manufacturing, technological innovations in Glue Laminating Machine are focusing on data-driven and intelligent optimization. Future Glue Laminating Machine will be more intelligent, integrating AI technologies and machine learning algorithms to achieve comprehensive production process optimization.
Integration of AI and Machine Learning: Future Glue Laminating Machine will leverage AI and machine learning technologies for in-depth production data analysis, enabling predictive adjustments and optimizations in the production process. Through continuous learning and adjustment, the equipment will better adapt to complex and variable production environments, enhancing overall efficiency and product quality.
IoT and Remote Monitoring: Combining IoT technology, future Glue Laminating Machine will enable remote monitoring and management. Production managers can view equipment status, production progress, and quality data in real-time through mobile devices, allowing for timely adjustments and optimizations that enhance flexibility and responsiveness in production management.
Equipment Upgrade Recommendations
For Glue Laminating Machine already in use, companies can further enhance their automation and intelligence levels through software upgrades or hardware modifications. For example, upgrading PLC control programs, adding intelligent sensors, or introducing data analysis modules can achieve higher production efficiency and finer quality control on the existing equipment.
Conclusion
With advanced automation technology and intelligent control systems, Glue Laminating Machine significantly improve production efficiency and product quality in battery manufacturing. Features such as real-time data monitoring, automatic adjustments, and fault self-diagnosis provide robust technical support for the production process. As AI and IoT technologies continue to evolve, Glue Laminating Machine will demonstrate greater potential in smart manufacturing, offering essential support for the production upgrades of enterprises.
FAQ
Q1: What are the advantages of the intelligent control system of the adhesive forming machine?
The intelligent control system of the adhesive forming machine offers real-time data monitoring, automatic adjustments, and fault self-diagnosis, which improve production precision, reduce defect rates, and ensure efficient and stable equipment operation.
Q2: Can the automation level of the equipment be further enhanced?
Yes, by upgrading software and hardware, such as introducing more advanced PLC controllers and intelligent sensors, the automation level of the equipment can be further enhanced, making it smarter and more efficient.
Q3: How does the adhesive forming machine perform fault self-diagnosis?
The equipment has a built-in fault self-diagnosis module that monitors its operational status through sensors. When an anomaly is detected, the system automatically triggers an alarm and stops the machine to protect both the equipment and the operator.
Q4: Can the operational status of the adhesive forming machine be monitored remotely?
Future Glue Laminating Machine will integrate IoT technology, enabling remote monitoring and management. Production managers can use mobile devices to view equipment status and production data in real time.
Q5: How does the adhesive forming machine optimize the production process?
The intelligent control system of the adhesive forming machine can automatically adjust operational parameters based on real-time production data. By using AI and machine learning technologies to analyze the data deeply, the machine continuously optimizes the production process.