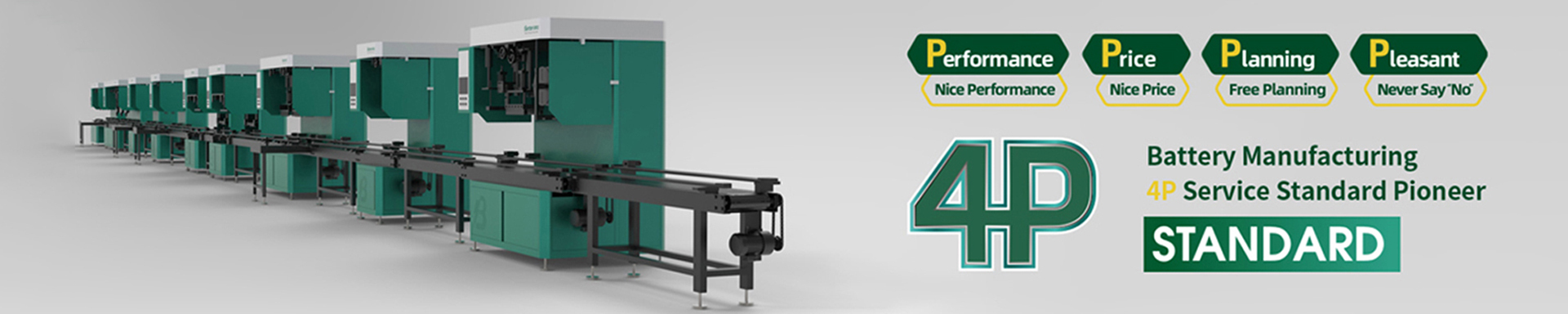
Application and Advantages of the Adhesive Forming Machine in Various Battery Manufacturing
2024-09-05 18:00Application and Advantages of the Adhesive Forming Machine in Various Battery Manufacturing
Introduction
With the development of the new energy industry and the continuous advancement of battery manufacturing technology, the adhesive application process has become a crucial step in battery production. The adhesive forming machine, an integrated piece of equipment with multiple automation technologies, not only improves production efficiency but also enhances product consistency and quality. This article will explore the application and advantages of the adhesive forming machine in the manufacturing of different battery types.
Application in Pouch Batteries
Pouch batteries, known for their lightweight, flexible design, and high energy density, are widely used in consumer electronics and electric vehicles. In the manufacturing of pouch batteries, the adhesive application process is essential for the battery’s sealing and safety. Traditional manual adhesive application methods often suffer from low precision, low efficiency, and high defect rates. In contrast, the adhesive forming machine, with its precise automated control system, ensures uniform adhesive application on each battery, reducing the occurrence of bubbles and wrinkles, thus enhancing the battery’s sealing and safety performance.
Moreover, the adhesive forming machine can automatically complete adhesive film cutting, application, and waste adhesive recycling, achieving full-process automation and significantly reducing manual operation time and error rates. This is especially important for pouch battery manufacturers with fast-paced production and high-volume demands.
Potential Applications in Cylindrical and Prismatic Batteries
Although adhesive forming machines are primarily used in pouch battery production, their applications in other battery types are also being explored as technology evolves. For example, in the manufacturing of cylindrical and prismatic batteries, while the adhesive application process may not directly involve the battery casing, the precise control and efficient application characteristics of the adhesive forming machine can still be valuable in steps like applying protective films on electrodes or wrapping insulating tapes.
Through appropriate technical adjustments and mold replacements, adhesive forming machines can adapt to different shapes and sizes of batteries, providing greater flexibility for production lines. This adaptability is particularly beneficial for the production of new and customized batteries, where the adhesive forming machine can offer effective technical support to meet diverse manufacturing needs.
Advantages: Efficiency, Precision, and Adaptability
·
High Production Efficiency: The adhesive forming machine integrates multiple automated process modules, from feeding, adhesive application to discharging, with no need for manual intervention, achieving efficient continuous production. Its multi-station design can simultaneously handle multiple battery units, significantly boosting production efficiency.
·
·
Precision Control: Equipped with high-precision sensors and control systems, the machine can monitor various parameters in the adhesive application process in real-time, ensuring precise operation every time. This high level of control not only reduces the defect rate but also ensures the quality consistency of each battery.
·
·
Strong Adaptability: The modular design and flexible adjustment features of the adhesive forming machine enable it to quickly adapt to the production requirements of different battery types. Whether it involves adjusting sizes or changing adhesive film materials, the machine can complete adjustments in a short time, reducing downtime and improving production line utilization.
·
Customer Case Study: Application Example
A well-known battery manufacturing company experienced a 30% increase in production efficiency and a defect rate reduction to below 1% after introducing the adhesive forming machine in their pouch battery production. The integration of this equipment not only optimized the production process but also significantly enhanced the product's market competitiveness. The company recouped the equipment investment costs within a few months and secured more customer orders due to the higher production efficiency.
Through this technological upgrade, the company not only achieved significant improvements in production efficiency but also gained a greater competitive edge in the market. This fully demonstrates the enormous potential and application value of adhesive forming machines in modern battery manufacturing.
Conclusion
The application of adhesive forming machines in battery manufacturing is not limited to the adhesive application process of pouch batteries; they also show potential in the production of cylindrical and prismatic batteries. With characteristics of efficiency, precision, and adaptability, adhesive forming machines provide strong technical support to battery manufacturers, helping them stand out in the highly competitive market.
FAQ
Q1: Is the adhesive forming machine only used for pouch batteries?
A: While the adhesive forming machine is mainly used for the adhesive application process in pouch batteries, with suitable technical adjustments and mold changes, it can also be applied to certain processes in cylindrical and prismatic batteries.
Q2: How automated is the equipment?
A: The adhesive forming machine is highly automated, capable of completing the entire process from feeding to discharging, greatly reducing manual intervention and operational errors.
Q3: How much can the defect rate be reduced by using the adhesive forming machine?
A: According to real application cases, the precise control system of the adhesive forming machine can reduce the defect rate to below 1%, significantly decreasing material waste and production costs.
Q4: Is the equipment adjustment complex?
A: The modular design and user-friendly interface of the adhesive forming machine make adjustments relatively simple, allowing the machine to quickly adapt to the production needs of different battery types and sizes.
Q5: What is the typical investment payback period for the adhesive forming machine?
A: Depending on the production scale and equipment model, the investment payback period is usually within one year, but it varies according to the specific production conditions of the enterprise.