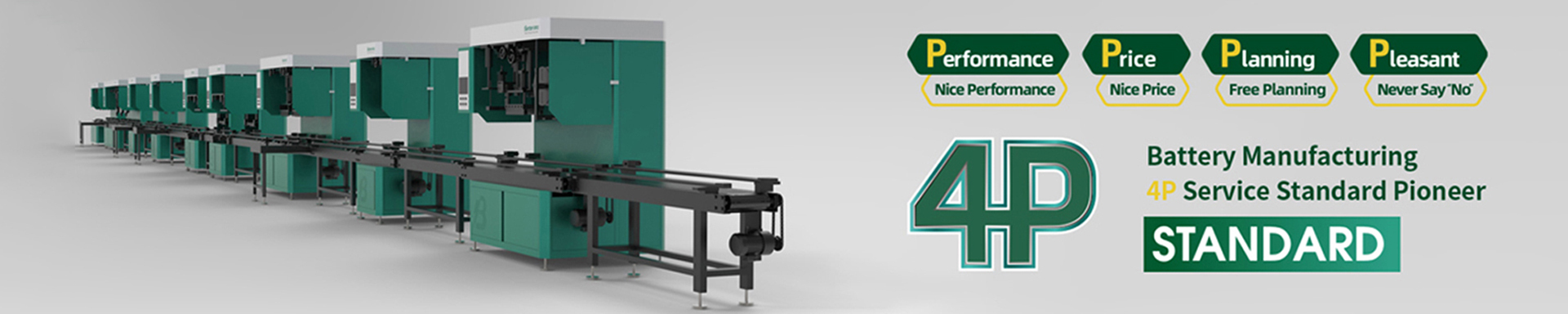
Application of Laser Welding Machines in Battery Manufacturing: A Tool to Enhance Efficiency and Quality Introduction
2024-09-04 18:00As a core industry of modern technology, the battery manufacturing sector is undergoing significant transformations amid the global industrialization process. With the rapid proliferation of electric vehicles, energy storage systems, and consumer electronics, the battery manufacturing industry faces unprecedented challenges and opportunities. In this highly competitive market, manufacturers are constantly seeking advanced technologies that can enhance production efficiency and ensure product quality. Laser welding machines, as a cutting-edge technology, are gradually becoming an essential tool for battery manufacturing enterprises.
Challenges in the Industry
Currently, the battery manufacturing industry faces several key challenges:
· Low Production Efficiency: Traditional welding techniques often rely on manual operations, resulting in low efficiency and difficulty meeting the demands of large-scale production.
· Quality Control Difficulties: In battery production, welding quality directly impacts battery performance and safety. Traditional welding methods struggle to guarantee precision and consistency, often leading to poor internal connections that affect overall product quality.
· High Production Costs: Manual welding not only incurs high labor costs but also tends to produce defective products, increasing subsequent repair and quality control expenses.
In response to these challenges, battery manufacturers urgently need a solution that can improve production efficiency, ensure welding quality, and reduce production costs. Laser welding machines have emerged as the ideal solution under these circumstances.
How Laser Welding Machines Address These Challenges
Automation
A notable advantage of laser welding machines is their high level of automation. Traditional welding equipment usually requires skilled operators, which increases labor costs and limits production efficiency. Laser welding machines, on the other hand, operate through fully automated processes, from loading battery tabs and aligning positions to completing the welding, all without manual intervention. This not only significantly reduces human error but also greatly enhances overall production line efficiency.
In large-scale production scenarios, laser welding machines can weld up to 70 pieces per minute, providing a significant competitive advantage for manufacturers needing to respond quickly to market demands.
Precision and Consistency
Welding precision and consistency are crucial in battery manufacturing. Weld points must be precise to ensure smooth current flow between cells. Laser welding machines utilize advanced laser technology, achieving a welding precision of ±0.01mm, which means each weld point is placed exactly at the designated position.
Additionally, laser welding machines ensure consistent welding quality across all batteries. This consistency significantly reduces product rejection rates caused by poor welding, thereby further lowering production costs. For battery manufacturers striving for exceptional quality, this high-precision and high-consistency welding process is a critical competitive edge.
Cost Efficiency
By enhancing production efficiency and reducing defect rates, laser welding machines significantly lower production costs for enterprises. Although the initial investment in laser welding machines is relatively high, the cost savings achieved through reduced labor costs, lower defect rates, and improved product quality make the return on investment quite attractive.
In the long run, laser welding machines not only help companies stand out in a competitive market but also provide strong support for sustainable business growth.
Case Studies of Success
To better understand the value of laser welding machines in battery manufacturing, let's look at some real-world examples:
A well-known electric vehicle manufacturer encountered numerous issues with traditional welding methods, including low production efficiency, unstable welding quality, and high production costs. After introducing laser welding machines, the company saw a 30% increase in production efficiency and a 50% reduction in welding defects. The automation processes significantly enhanced welding precision, ensuring the overall quality and safety of the batteries. Furthermore, due to the non-contact nature of laser welding, no excess mechanical stress is generated during the welding process, which extends the lifespan of the batteries.
Another example comes from the consumer electronics sector. A company producing high-end smartphones introduced laser welding machines, which not only resolved the issue of insufficient production capacity but also significantly improved product quality through high-precision welding processes, earning high praise in the market.
These successful applications validate the exceptional performance of laser welding machines in the battery manufacturing industry and offer valuable references for other companies.
Conclusion
In the fiercely competitive global battery manufacturing industry, laser welding machines, with their efficient, precise, and automated characteristics, are becoming the preferred equipment for more and more manufacturers. They not only help companies address challenges like low production efficiency, difficult quality control, and high production costs but also provide strong support for sustainable business development.
As technology continues to advance, the application scope of laser welding machines will expand further, and their importance in battery manufacturing will become increasingly evident. For companies seeking to improve production efficiency and product quality, laser welding machines are undoubtedly an ideal choice.
Act now and introduce laser welding machines to transform your production line and embrace the new era of intelligent manufacturing!
FAQ
Q1: What are the main advantages of laser welding machines compared to traditional welding methods?
A: The main advantages of laser welding machines are their high precision and automated operation capabilities. They can achieve a welding precision of ±0.01mm and reduce human errors through automated processes, significantly improving production efficiency and product quality.
Q2: Will laser welding machines damage the internal structure of batteries?
A: No. Laser welding technology focuses energy, resulting in a small heat-affected zone that enables efficient welding without damaging the internal structure of the battery.
Q3: Are maintenance costs for laser welding machines high?
A: Although the initial investment in laser welding machines is high, maintenance costs are relatively low. The equipment features self-diagnostic functions and remote maintenance capabilities, effectively reducing downtime and repair expenses.
Q4: What types of batteries are suitable for laser welding machines?
A: Laser welding machines support various battery specifications and are suitable for manufacturing different types of batteries, ranging from consumer electronics to electric vehicle batteries.