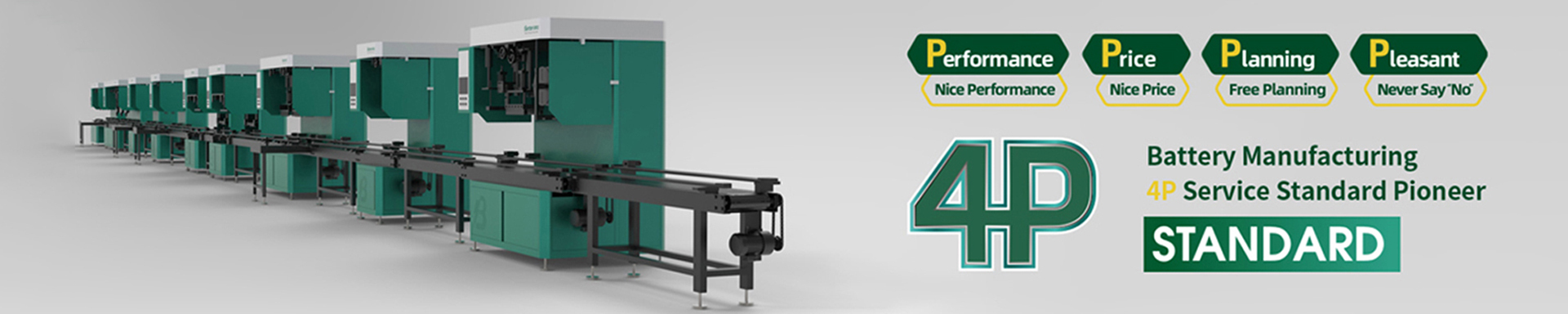
What machine is used to make a battery?
2025-03-04 18:00The battery manufacturing process involves various specialized machines that ensure the efficient production of high-quality batteries. Whether you’re manufacturing lead-acid batteries, lithium-ion cells, or other types of rechargeable batteries, the machinery involved plays a crucial role in ensuring that the batteries meet required standards for performance and safety. In this article, we will focus on the machines used in the production of lead-acid batteries, particularly the battery making machine, **lead-acid battery making machilead-acid battery making machine, lead-acid battery manufacturing machinery, and how these machines are designed to meet the needs of modern battery producti.
Types of Machines Used in Battery Manufacturing
Battery manufacturing is a complex, multi-step process that requires precise automation and high-quality machinery. Different machines are used at each stage of production, and the specific machinery selected can si
1. Battery Plate Production Machines
The production of battery plates is a key first step in the manufacture of lead-acid batteries. Pla
Lead Oxide Production Machine: This machine processes lead into lead oxide, which is used
Plate Casting Machine: This machine casts the lead into the form of plates. It ensures precise dimensions and uniform t
2. Lead-Acid Battery Making Machine: Plate Stacking Machine
Once the plates are made, they need to be stacked to form the internal structure of the battery. This is where the lead-acid battery making machine plays an essential role.
Plate Stacking Machine: This machine automatically stacks the positive and negative plates along with the separators to create the basic structure of the battery. Plate stacking must be highly accurate to ensure the battery’s performance and longevity.
3. Electrolyte Filling Machines
After stacking the plates, the next crucial step is filling the battery with the electrolyte, typically a sulfuric acid solution, which enables the electrochemical reaction within the battery. The lead-acid battery making machine used for this task must ensure precision in the amount of electrolyte that is added to each cell.
Electrolyte Filling Machine: These machines fill the battery with electrolyte in a controlled manner. The precise filling ensures that each cell is filled to the correct level, which is critical for battery performance. Inaccurate filling can lead to inefficiency and potential damage to the battery.
4. Sealing and Closing Machines
Sealing the battery after electrolyte filling is crucial to ensure that no leakage occurs and that the battery remains safe to use. The battery making machine used in this phase is designed to securely close and seal the battery casing.
Sealing Machine: These machines tightly seal the battery’s terminals and casing to prevent any leakage of electrolyte. Sealing is a vital step in ensuring the battery’s safety and longevity.
5. Formation and Charging Machines
After assembly, the battery needs to undergo a process known as formation, where it is charged and discharged to activate the electrochemical reactions inside the cells. The lead-acid battery making machine used for this step is responsible for carefully controlling the voltage and current during the charging process.
Formation Machine: The formation machine charges the battery cells to initiate the chemical reactions within the plates. This is a crucial step to ensure the battery functions effectively when used in real-world conditions. The formation process also helps in determining the battery’s capacity and ensures that all cells are functioning correctly.
6. Testing Machines
Testing is a critical part of the battery manufacturing process to ensure that each battery meets the required standards. Lead-acid battery manufacturing machinery used in testing can detect defects or performance issues that may arise during production.
Testing Machine: After the formation process, the batteries go through various tests, such as capacity testing, voltage testing, and discharge testing. These machines ensure that the battery performs at optimal levels and meets the necessary quality standards for safety and efficiency.
7. Packaging and Final Assembly Machines
Once the batteries are fully formed, tested, and sealed, they move to the final stage of production, where they are packaged for shipping. This is where the battery making machine helps automate the final steps.
Packaging Machine: This machine is responsible for securely packaging each battery before shipping. It ensures that the batteries are handled properly to prevent damage during transit.
Key Features of Lead-Acid Battery Manufacturing Machinery
The lead-acid battery manufacturing machinery used today is designed for efficiency, automation, and precision. Some of the standout features of modern battery making machines include:
1. High Automation
Modern lead-acid battery manufacturing machinery is highly automated, meaning that many of the processes—such as plate stacking, electrolyte filling, and testing—are carried out with minimal human intervention. This reduces the risk of human error and improves production speed, ensuring that each battery is produced consistently.
2. Precision Control
The machinery is designed to ensure precise control over important aspects such as electrolyte filling and plate alignment. This precision is essential in achieving the desired battery capacity and performance. Automated systems can monitor and adjust the machinery in real-time to ensure consistency.
3. Safety Features
Lead-acid batteries contain hazardous materials such as sulfuric acid, so safety features are a key consideration in manufacturing. The machines are designed to comply with industry safety standards, and many are equipped with sensors and alarms to prevent accidents such as acid spills or short circuits.
4. Energy Efficiency
Energy consumption is an important consideration in battery manufacturing. Modern machinery is designed to be energy efficient, helping manufacturers reduce operational costs while still meeting production targets. The machines are built to consume the minimum amount of energy required for each stage of the process.
5. Scalability
Many battery making machines are scalable, meaning they can be adjusted to suit the production needs of both small and large-scale manufacturers. Whether you're just starting out or running a high-volume factory, scalable machines can help optimize production based on your capacity requirements.
Lead-Acid Battery Manufacturing Process: The Role of Efficient Machinery
The lead-acid battery making machine plays an integral role in every step of the production process. From the initial lead oxide production to the final sealing and testing, these machines ensure that the manufacturing process runs smoothly and efficiently. By using automated systems and high-tech machinery, manufacturers can achieve high levels of quality control and productivity. Automation also ensures that lead-acid batteries meet stringent performance and safety standards.
Conclusion
Manufacturing lead-acid batteries requires a series of specialized machines, each serving a vital function in the production process. From the battery making machine used to stack plates to the lead-acid battery manufacturing machinery that fills electrolytes and tests battery performance, each piece of equipment contributes to the overall success of the production line. With modern, automated machines, manufacturers can enhance efficiency, maintain quality, and scale their production to meet growing demand. Whether you’re setting up a new factory or upgrading an existing production line, investing in high-quality battery-making machinery will help ensure that your lead-acid batteries perform reliably and safely in a wide range of applications.