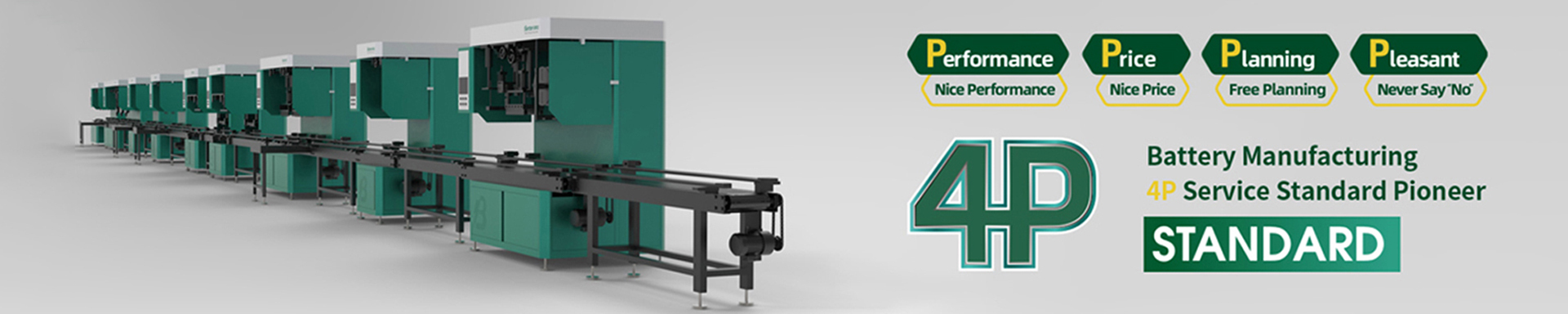
One minute to decrypt the main process flow and equipment for the complete production of lead acid batteries
2022-05-24 18:50Lead-acid battery is mainly composed of positive/negative plate group, separator, battery container, electrolyte, battery cover, etc. The electrode is mainly made of lead and lead oxide, and the electrolyte is sulfuric acid solution. In the discharge state, the main component of the positive electrode is lead dioxide, and the main component of the negative electrode is lead. In the charge state, the main components of the positive and negative electrodes are lead sulfate. At present, lead-acid batteries still occupy most of the global battery market, but most people do not have a good understanding of the "main process and equipment of lead-acid batteries". This article will analyze and decrypt them.
1. Lead powder manufacturing
Use lead oxide mill to processed the electrolytic lead into lead powder that meets the requirements of battery production through oxidation screening. The main components of lead powder are lead oxide and metallic lead. The quality of lead powder is closely related to the battery manufactured.
The Shimadzu method is mostly used in China to produce lead powder, while the Barton method is used in Europe and the United States.
The process of producing lead oxide by the Shimadzu method is briefly described as follows:
First step: Processed qualified electrolytic lead into lead ball or lead segment of a certain size through casting or other methods;
Second step: Put the lead ball or lead bar into the lead oxide mill, and oxidation to lead oxide.
Third step: Storage the lead powder into the storage silo for about 2-3 days, and use after testing.
Main equipment of lead oxide mill: lead cylinder caster (lead ingot cutting machine), ball mill, oxide filling machine, conveying and storage system.
Main parameters of lead oxide: oxidation degree; apparent density; water absorption; particle size, etc.
Lead Oxide Manufacturing Machine
2. Grid casting
The grid is the carrier of the active material and the main support for the internal plates of the battery. It is grid-shaped. In addition to support, the most important thing is the conductive function. Vented battery grids are generally casted with lead-antimony alloys, maintenance-free battery grids are generally casted with low antimony alloys or lead-calcium alloys, and sealed valve-regulated lead-acid battery grids are generally casted with lead-calcium alloys.
First step: Choose the lead alloy according to your battery type and melt it in the lead pot, pour the melt lead into the mold. After cooling, cut and stack the grid.
Second step: Place the grid after cutting and brushing for a period of time and send it to next process.
Main equipment of grid casting: lead ingot melting pot, grid casting machine and its mold.
Main parameters of grid: quality, thickness, completeness, size and etc.
Lead Grid Casting Machine
3. Plate production
Battery plate is the main part of the lead acid battery, and its quality will directly affect the battery performance.
The process of producing pasted plate as follow:
First step: Mix lead power, dilute sulfuric acid, additives by paste mixer to make lead paste.
Second step: Paste the lead paste on the grid by pasting machine or manually operate.
Third step: Curing and drying the battery plate after pasting, and you will get the uncharged plate.
Main equipment of plate production: paste mixer, pasting machine, flash drying machine, curing and drying system.
Main parameters of uncharged plate: formula of lead paste, apparent density, acid content, plate weight, thickness, free lead content, moisture content, etc.
4. Assembly process
The battery assembly has a big difference between the car battery and the sealed valve-regulated lead-acid battery. The assembly process is to assemble different types and different numbers of plates into various types of batteries according to different requirements. The assembly of sealed valve-regulated lead-acid batteries generally use AGM separators, while car batteries generally use PE separators.
The process of assembly as follow
First step: Envelop and stack the battery plate into plate group and load the plate group into the welding tooling.
Second step: Place the cast welding or manual welding plate group into the clean battery container.
Third step: The car battery needs inter-cell welding and heat sealing before finished. If the sealed valve-regulated lead-acid battery use ABS battery container, it needs to be seal by special adhesive (epoxy resin).
Main equipment of battery assembly process: Car battery, motorcycle battery, small, middle and large sealed valve-regulated lead-acid battery assembly line, automatic battery assembly line.
Main parameters of battery assembly: enveloping quality, busbar welding quality and material, short circuit performance, inter-cell welding quality, sealing performance, positive and negative terminal performance, etc.
5. Formation process
Plate formation and battery formation are two different methods of battery manufacturing, can be selected according to specific conditions.
Plate formation is generally easier, but the maintenance cost is high, and environmental pollution needs special treatment.
The quality control of battery formation is harder. Cost is lower but have high quality requirements of the uncharged plate quality.
The process of sealed lead-acid battery formation as follow:
First step: Load the qualified uncharged plate into the battery container and seal.
Second step: Fill a certain concentration of dilute sulfuric acid into the battery according to the specified amount.
Third step: Place the battery after filling the acid for a while and charge the battery according to the specified current. Generally, the battery will need discharge testing after formation before storage in storehouse and ready to sale.
Main equipment of battery formation process: charge and discharge machine, etc.
Main parameters of battery formation: acid filling volume, acid density, acid temperature, charging process setting, voltage, density after formation, etc.
“Good battery quality required good machine”, Better (Xiamen) Power Technology Co., Ltd. focus on lead acid battery production equipment, material and component, which is a rare lead-acid battery equipment manufacturer and complete equipment supplier with the most complete equipment and the most experienced industry in China. At present, it is the first place in China's domestic lead-acid battery industry for integrated resource operation and export. It has exported more than 3,000 equipment (excluding auxiliary materials, raw materials, batteries, etc.) and business has cover more than 70 countries.
Since entering the industry field after its establishment in 2012, Better (Xiamen) Power Technology Co., Ltd. has gradually developed from a single equipment supplier to a business model of general contracting integration services such as R&D and design, project construction, complete equipment, installation and commissioning. In this way, it has successfully avoided the problem of customers who purchase equipment from multiple equipment suppliers and then install them together, because a dispersed supply relationship is not transparent enough in quality and price. And it is possible to lead to problems such as long construction cycle, heavy technical docking tasks, cumbersome business communication, and poor interaction between the front, middle and finish stages. However Better (Xiamen) Power Technology Co., Ltd. provides customers with high-end lead-acid battery manufacturing equipment and turnkey solutions for complete sets of equipment. From pre-sales, in-sales, and after-sales, there is only one service provider from Better, which can solve these problems well. Promote rapid delivery, allowing battery manufacturers to quickly increase production.