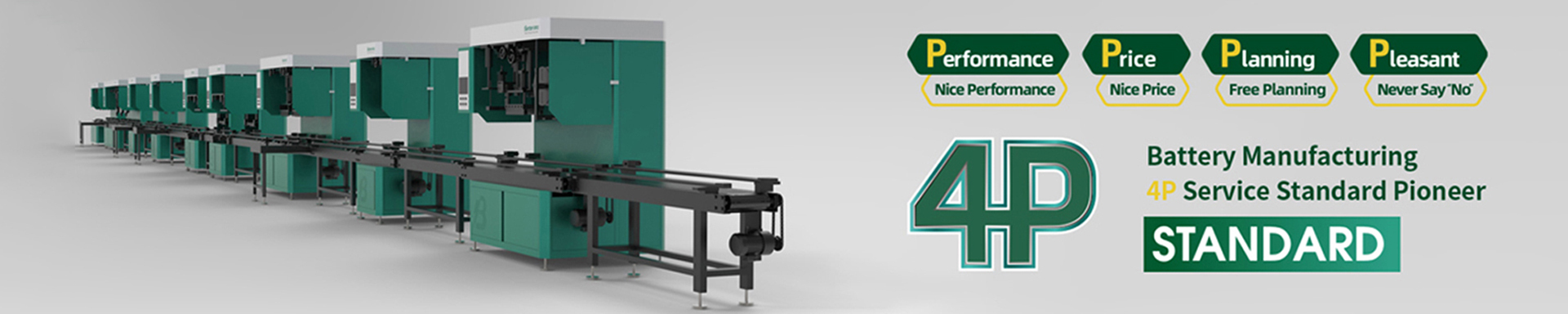
Lead Acid Battery Basic Structure and Fundamentals
2023-08-05 18:00In the last two years, even though lithium batteries are very popular in the market, in the electric tricycle sector, for quite a long time, there is no doubt that lead-acid battery will maintain its dominance in market competition.
In other words, lead-acid batteries are the root of electric tricycles. As an electric tricycle industry insider, today I'm going to tell you more information about the lead-acid battery structure and fundamentals.
Lead-acid batteries are composed of important parts such as positive and negative plates, separators, plastic containers, poles and safety valves. The nominal voltage of each single cell is 2V, so a 6V or 12V pneumatic lead-acid battery is generally composed of 3 or 6 cells in packs. A set of independent cells are assembled in packs to form a compete battery to work as automotive power.
Here's a specific look at the components of a lead-acid battery.
1. Battery Plate Group
The battery plate group is the core part of the battery because its role is to receive the charged electrical energy and release the outward electrical energy, which is divided into two kinds of positive and negative plates. The plate is composed of grid and active material. Thin plate has higher specific capacity (the capacity provided by the size of the plate) and improves the performance for starter. The charging and discharging process of the battery is achieved by the electrochemical reaction between the active substances on the plates and the electrolyte.
The role of the grid is to accommodate the active substances that are pasted together to form the plate, and the material of the grid is mostly lead-antimony alloy which contains 5%-7% lead. By adding lead into the gird, we can improve the casting performance and mechanical strength, but it will accelerate the precipitation of hydrogen, resulting in automatic discharge, which will eventually lead to rapid consumption of electrolyte and short service life of the battery.
The active substance is the main component in the electrochemical reaction. When the formation process is complete (the transformation process of active substances on the positive and negative plates is called formation process), the porous lead dioxide (PbO₂) the active substances on the surface of positive plate mostly will turn reddish-brown and the spongy pure lead (Ph) will have greyish-bronze color.
Get positive and negative plates both immersed in the electrolyte, you can get 2V electromotive force (e.m.f.) and in order to increase the capacity of the battery, we often put more positive and negative plates into the battery container to assemble one large-capacity cell. Due to the poor mechanical properties of the positive plate, when the battery is being activated, there will be some differences between the two sides of plates. The inconsistency will cause the arching-like deformation or the shedding of the active substances. That’s the reason why we always put an extra negative plate inside a cell to balance the electric discharge.
2. Battery Separator
The role of the battery separator is to separate the positive and negative plates immersed in the sulfuric acid solution. In order to reduce the volume of the battery, positive and negative plates should be put together closely. Besides we should make sure that positive and negative plates are separated by the insulating layers which are usually made of rubber, plastic, glass, fiber and other insulating materials.
Except playing an insulating role between the positive and negative plates, it helps enable the positive and negative ions in the electrolyte to pass through smoothly, slow down the shedding of the active substances of the positive and negative plates, and prevent the positive plates from vibration damages. So it is required that the separator should meet such standards: 60% airhole coverage, small aperture, acid-resistant features, containing non-hazardous substances, sturdy, having low resistance in electrolyte with a characteristic of chemical stability, etc. The side with grooves must be perpendicular to the bottom of the battery container while assembling the battery because positive plate chemical reaction gets violent during charging and discharging process. The grooves enable the electrolyte to flow up and down smoothly and allow the air bubbles to circulate upwards or downwards, and store the shedding part of the active substances.
In recent years, some manufacturers have also produced some envelope-shaped separators to cover the positive plate, which can effectively prevent the shedding of the active substances.
3. Electrolyte
Electrolyte can prompt the ionization of the active substances of the plates to generate the electrochemical reaction. The electrolyte is composed of battery-specialized sulfuric acid and distilled water in a certain proportion. The general automotive lead-acid battery electrolyte is dilute sulfuric acid with the density of (1.280±0.010) g/cm³ (25℃).
The density of the electrolyte has a great influence on the performance and service life of the battery. In order to increase the capacity of the battery and reduce the freezing point of the electrolyte, it is necessary to increase the density of the electrolyte. However, higher density will lead to increased viscosity, which will reduce the capacity of the battery. Besides, it is necessary to specify the density value of the electrolyte under different climatic conditions.
Generally, for every 1℃ change in temperature, the density changes by 0.0007g/cm³. When the temperature of the electrolyte increases, the density decreases; when the temperature decreases, the density increases. Therefore, the temperature is a prerequisite for determining the density value of the electrolyte. Countries around the world have stipulated the standard temperature for electrolyte, and in that case, our country is 15℃, Japan 20℃, Europe and the United States are 25℃ and 30℃ respectively.
4. Battery Container
Battery container are used to contain the electrolyte and plates, so the shape of it is usually long cubic, separated into 3 or 6 single-cell troughs. On the top edge of the cell troughs are special groove pattern for connecting the container with the cover and on the bottom of the container are some convex strips to support the plate group.
Rubber and polypropylene plastic are two main materials to produce battery containers. Rubber container is featured with acid-proof, heat-proof, cold-proof, vibration-proof, insulation and considerable good mechanical strength and other advantages, but the container wall is thicker, generally 10mm; polypropylene plastic container is not only acid-resistant, heat-resistant, vibration-resistant, but also high-strength, high toughness, high-quality, smaller, thinner, generally speaking 3.5mm. Besides, the shape and the appearance is elegant, transparent, easy for heat-sealing and producing, so polypropylene-plastic-made containers have come into vogue in recent years.
Single-cell battery’s acid intake covers are usually designed with an opening for expelling the hydrogen and oxygen produced by electrolysis of water during battery charging process lest gas would accumulate and make its internal pressure rise up, resulting in container cracking or even an explosion. In addition, we can also install the oxygen filter around the opening in order to prevent water vapor escaping and reduce the water loss.
5. Safety Valve (for venting)
Safety valve is a key component of the valve-regulated battery because the quality of the safety valve directly affects the service life, uniformity and safety of the battery. According to the relevant standards and the use of valve-regulated batteries, the safety valve should meet the following technical conditions:
(1)Turn on the valve unidirectionally.
(2) Unidirectional sealing: to prevent air penetrating into the interior of the battery.
(3)The difference between the opening and closing pressures of the safety valves of the same group of batteries shall not exceed 20% of the average value.
(4)Battery service life should at least last for 15 years.
(5)Filtering function: to prevent the acid or acid mist from escaping through the safety valve.
(6)Explosion-proof: the interior of the battery should be explosion-proof when the outside of the battery is exposed to an open flame.
(7)Vibration-resistant: during transportation and use, the safety valve won’t get loose from vibration and repeated opening and closing action.
(8)Acid-resistant
(9)High and low temperature resistant
6. Others
In addition to the major components listed above, there are terminal wire connector, intercell connector and other accessories.
Single-function battery discharging device is only for discharging process and cannot be charged, so the battery needs to be charged in advance, then discharged, so that the cost of charging and discharge testing will be relatively cheaper.
Charging and discharging machine AIO device is convenient and helpful!