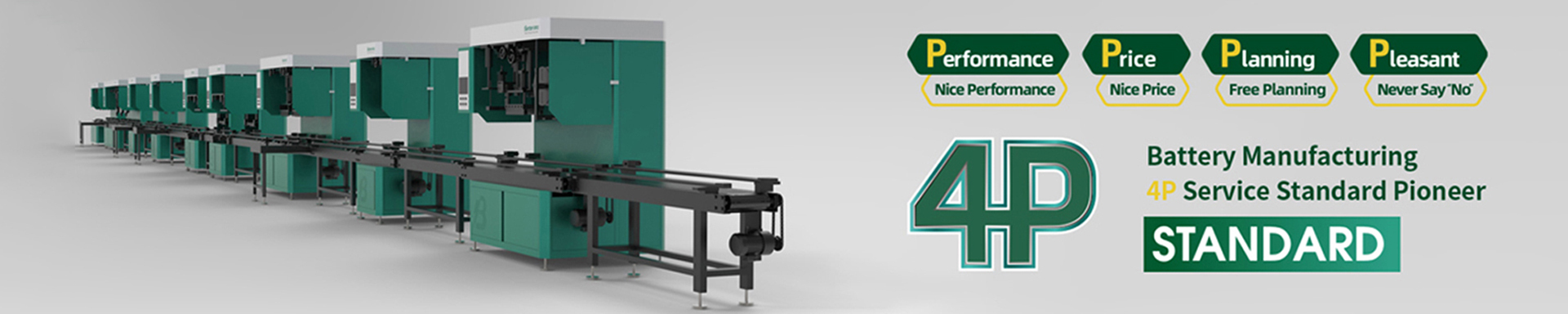
Application and Advantages of Double-Sided Labeling Machines in Battery Production
2024-09-12 18:00Introduction
As battery production technology continues to advance, the requirements for labeling processes have also increased. The double-sided labeling machine, a highly efficient automation device designed specifically for battery production, can simultaneously label both sides of the battery, significantly improving production efficiency while ensuring uniformity and precision in labeling quality. This article explores the specific applications and notable advantages of double-sided labeling machines in battery production, helping companies better understand how this equipment optimizes production processes.
I. Double-Sided Labeling Requirements in Battery Production
Labeling is an essential step in battery production. Labels are used not only for product identification but also to provide information and ensure product quality. For example, labeling both sides of the battery with ultrasonic labels, forming labels, or PET films can prevent leakage, enhance insulation performance, and protect battery components from external environmental impacts. However, traditional manual or single-sided labeling methods are not only inefficient but also prone to inaccuracies, such as incorrect label placement or poor adhesion, which can negatively impact product quality and production efficiency.
II. Advantages of Double-Sided Labeling Machines
·
High-Efficiency Double-Sided Labeling: The double-sided labeling machine, equipped with precision mechanics and intelligent control systems, can complete labeling on both sides of the battery in a single operation. Compared to traditional single-sided labeling equipment, the double-sided labeling machine can cut labeling time in half, significantly boosting production efficiency. The machine’s labeling speed can exceed 1,000 pieces per hour, making it highly suitable for large-scale battery production lines.
·
·
Precise Labeling Control: The double-sided labeling machine uses high-precision sensors and positioning systems to ensure that each label is accurately affixed to the designated position. The equipment’s labeling precision reaches ±0.1 mm, far superior to manual operations or simpler mechanical devices. This high-precision labeling effectively reduces deviations and defects during the battery labeling process, improving product consistency and appearance quality.
·
·
Reduced Reliance on Manual Labor: Traditional labeling processes typically require a significant amount of manual labor, which is time-consuming, labor-intensive, and prone to human errors. The double-sided labeling machine minimizes manual operations through fully automated processes, reducing labor costs and minimizing product quality issues caused by operational errors. Additionally, the intelligent control system of the equipment can detect labeling effects in real time and adjust labeling parameters as needed, ensuring that each product meets quality standards.
·
·
Improved Product Pass Rate: In battery production, the quality of label adhesion directly affects the battery’s safety and performance. The double-sided labeling machine ensures that labels are firmly affixed to the battery surface through strict labeling control and stable equipment operation, preventing label detachment or movement during use. This advantage allows the double-sided labeling machine to significantly improve the product pass rate and reduce rework and waste.
·
III. Case Study Analysis
Case Background: A well-known battery manufacturing company introduced double-sided labeling machines on its production line, primarily for double-sided labeling of battery casings. The company previously relied on manual labeling, which resulted in low efficiency and inconsistent labeling quality. After introducing the double-sided labeling machine, the company saw significant improvements in both production efficiency and product quality.
Application Results:
· Increased Production Efficiency: By using the double-sided labeling machine, the company’s labeling efficiency improved by about 50%, leading to an overall increase in production line output.
· Stable Product Quality: Due to the equipment’s high-precision labeling, the product pass rate increased from 95% to over 99%, effectively reducing rework caused by labeling issues.
· Cost Reduction: The reduced reliance on manual labor not only lowered labor costs but also decreased the time and expenses involved in training new employees. The stable operation of the equipment also reduced the risk of unexpected downtime during production.
IV. Frequently Asked Questions (FAQ)
1. What types of batteries are suitable for double-sided labeling machines?
Double-sided labeling machines are suitable for various types of batteries, including cylindrical, prismatic, and pouch batteries. The equipment’s labeling positions and materials can be adjusted according to different battery specifications and requirements, ensuring adaptability to diverse production needs.
2. Can the labeling speed and precision of the equipment be adjusted?
Yes, the labeling speed and precision of the double-sided labeling machine can be adjusted based on actual production needs. The intelligent control system supports the setting of multiple labeling parameters, allowing users to easily adjust speed, pressure, and label positions via a touch-screen interface to achieve optimal labeling results.
3. Is maintenance of the equipment complicated?
Maintenance of the double-sided labeling machine is straightforward. Routine maintenance mainly includes cleaning sensors, checking the lubrication of mechanical parts, and regularly replacing worn components. The equipment comes with a detailed maintenance manual, allowing users to perform self-maintenance. Additionally, the manufacturer provides professional after-sales service to ensure timely technical support for complex issues.
4. How can long-term stable operation of the equipment be ensured?
To ensure the long-term stable operation of the double-sided labeling machine, it is recommended that users follow the daily maintenance guidelines and conduct necessary checks before each operation. Regular comprehensive inspections and calibrations of the equipment can help identify and resolve potential issues promptly, ensuring the machine consistently performs at its best.
Conclusion
With its high efficiency, precision, and automation, the double-sided labeling machine has become an indispensable labeling solution in battery production. It significantly improves production efficiency and product quality while reducing manual operations and error rates, saving companies substantial costs. In the highly competitive battery manufacturing industry, the double-sided labeling machine is undoubtedly an ideal choice for enhancing production line automation and product pass rates.