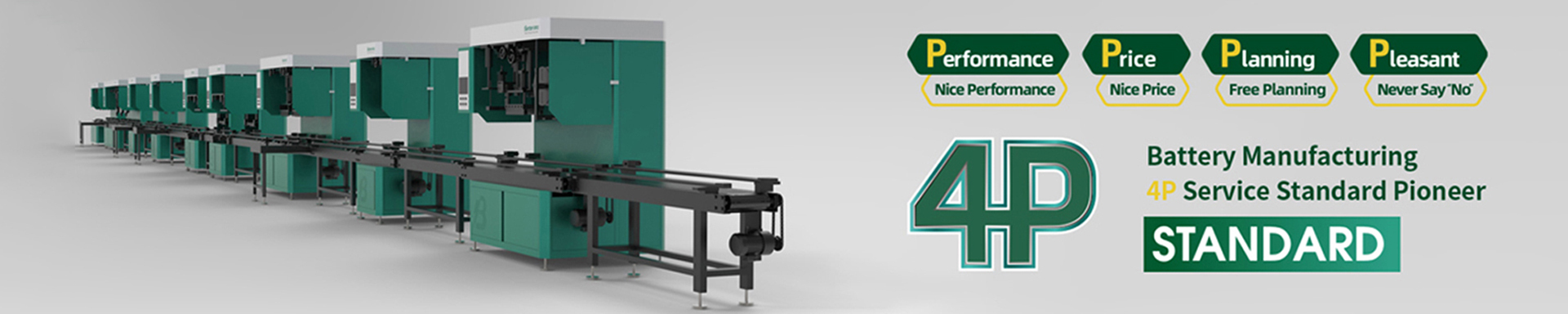
Maintenance and Common Fault Solutions for Glue Laminating Machine
2024-11-15 18:00Maintenance and Common Fault Solutions for Glue Laminating Machine
Introduction
Glue Laminating Machine, as efficient automated production equipment, significantly enhance production efficiency for battery manufacturing companies. However, to ensure the long-term stable operation and efficient production of these machines, daily maintenance and troubleshooting are essential. This article provides a detailed maintenance guide and shares solutions for common faults, helping companies maximize equipment performance and extend its lifespan.
Daily Maintenance Guidelines
Equipment Cleaning
Keeping the equipment clean is fundamental to ensuring its normal operation. Glue Laminating Machine generate adhesive film debris and dust during operation, which, if not cleaned promptly, may block sensors or affect the movement of machine parts. It is recommended to clean the surfaces and interiors of the equipment after each workday, especially in critical areas like the adhesive application module and sensor regions.
Key Component Inspection
Regular inspection of key components is an important measure to prevent faults. For Glue Laminating Machine, key components include sensors, drive motors, control systems, and adhesive film conveying devices. It is advised to check these parts weekly to ensure secure connections and normal operation. If abnormal noise, vibration, or operational issues are detected, immediate troubleshooting is necessary.
Replacement of Wear Parts
After prolonged operation, some wear parts may become worn or aged, affecting the machine's normal functioning. Common wear parts include adhesive film blades, conveyor belts, and motor belts. Companies should develop a replacement plan based on usage conditions to ensure sufficient spare parts are available for timely replacement, preventing downtime due to lack of parts.
Lubrication and Maintenance
Regularly lubricating the machine's moving parts ensures smooth operation. Particularly for frequently moving components like robotic arms and rails, lubrication can reduce wear and extend part life. It is advisable to conduct a comprehensive lubrication maintenance every month, adjusting the timing based on equipment operation frequency and environmental conditions.
Regular Calibration
To ensure the precision and consistency of adhesive application, regular calibration of the equipment is required. Calibration adjusts the machine's parameter settings to meet production process requirements. It is recommended to perform calibration quarterly to ensure optimal operating conditions.
Common Faults and Solutions
Adhesive Film Offset or Misapplication
Cause: This may result from sensor malfunctions, uneven film conveying, or incorrect parameter settings.
Solution: Check if the sensors are functioning properly and clear any debris that may affect them; inspect the operation of the film conveying device and adjust the machine's parameter settings to ensure accurate film application.
Wrinkles or Bubbles During Adhesive Application
Cause: Insufficient film tension, uneven application pressure, or mismatched application speed may lead to quality issues.
Solution: Adjust the film tension to ensure it remains flat during conveying; check the pressure settings of the application head and adjust them to appropriate levels; appropriately adjust the application speed according to production requirements to avoid quality issues caused by speed variations.
No Response After Equipment Startup or Interruption During Operation
Cause: This may be due to power issues, control system failures, or accidental activation of the emergency stop button.
Solution: First, check the power connection to ensure stable voltage; inspect the status of the control system for any alarm information and restart the system if necessary; verify that the emergency stop button has not been accidentally pressed.
Incomplete Automatic Removal of Waste Adhesive
Cause: Malfunctions in the removal device or blockages in the waste recovery system.
Solution: Check if the removal device operates smoothly and clear any potential blockages; inspect the waste recovery system for blockages to ensure smooth recovery of waste adhesive.
Abnormal Noise or Vibration
Cause: Loose or worn mechanical parts, potentially related to belts, gears, or bearings.
Solution: Inspect the mechanical connections of the equipment to ensure all bolts and fasteners are secure; check for wear on belts and gears, replacing them as needed; regularly lubricate bearings and similar components to reduce wear and noise.
1.
Preventive Maintenance
To reduce equipment failure rates and improve availability, preventive maintenance is crucial. Companies can develop a detailed preventive maintenance plan based on equipment operation data, including regular inspections, troubleshooting, and spare parts management. Through preventive maintenance, companies can detect and address potential issues in advance, avoiding production losses due to unexpected downtime.
Data-Driven Preventive Maintenance:
By integrating intelligent control systems and data monitoring functions, companies can implement data-driven preventive maintenance. Analyzing operational data helps identify trends in performance degradation, allowing for preventive measures before issues arise. This approach can significantly lower equipment failure rates and enhance production line stability.
Supplier Support
Technical support from suppliers is equally important during equipment maintenance. Companies should choose suppliers that provide comprehensive after-sales services, including equipment installation, operation training, troubleshooting, and spare parts supply. Maintaining good communication with suppliers ensures timely access to technical support and maintenance guidance, keeping equipment in optimal operating condition.
Conclusion
The stable operation of Glue Laminating Machine relies not only on the equipment's performance but also on daily maintenance and prompt troubleshooting. Through scientific maintenance and effective preventive measures, companies can extend equipment lifespan, lower operating costs, and ensure efficient and continuous production. Timely resolution of common faults and close collaboration with suppliers are also key to maintaining continuous and efficient operation.
FAQ
Q1: How often should the laminating machine be maintained?
A: Daily cleaning should be performed after each production session, key component inspections are recommended weekly, lubrication and calibration should occur monthly, with specific frequencies adjusted based on equipment usage.
Q2: How can problems be quickly diagnosed after a fault occurs?
A: Start by checking the power supply, control system, sensors, and mechanical parts step by step. Review alarm information and operational status; contact supplier technical support for professional repairs if necessary.
Q3: How can adhesive film offset faults be prevented?
A: Regularly check the status of sensors and film conveying devices to ensure they are functioning properly; adjust machine parameters to maintain adhesive accuracy; keep the film conveying path clean and unobstructed.
Q4: What are the common wear parts of the laminating machine?
A: Common wear parts include adhesive film blades, conveyor belts, and motor belts. These components are prone to wear with frequent use and should be replaced regularly.
Q5: How can preventive maintenance be conducted through data analysis?
A: Utilize the intelligent control system of the equipment to monitor and analyze operational data, identify trends in performance degradation, and take preventive measures before failures occur, such as adjusting parameters or replacing wear parts.