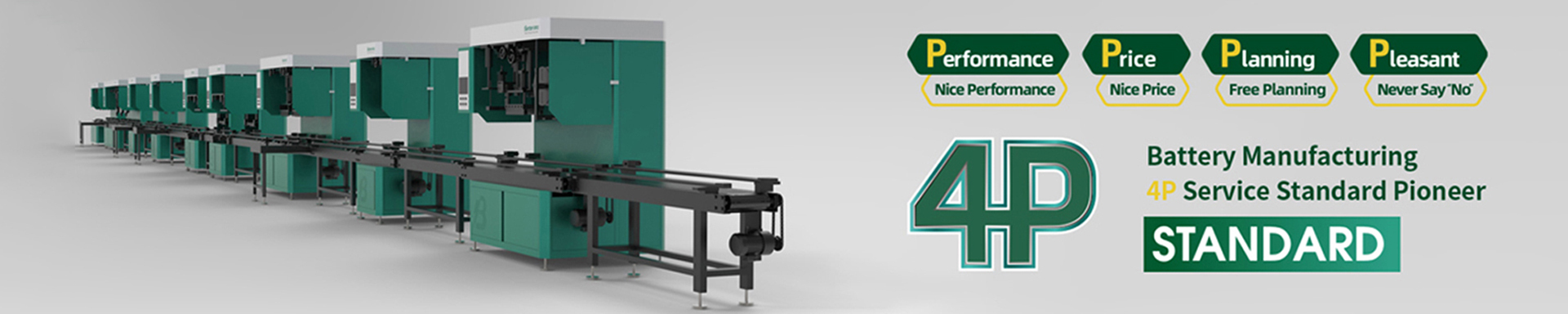
Analysis of the Intelligent Control System of the Double-Sided Labeling Machine
2024-10-09 18:00Introduction
In modern manufacturing, intelligent control systems are at the core of equipment automation and efficient operation. The double-sided labeling machine, with its advanced intelligent control system, achieves precise control and automatic adjustment of the labeling process. This not only improves production efficiency but also significantly reduces product defect rates. This article provides an in-depth analysis of the intelligent control system of the double-sided labeling machine, including its components, working principles, and advantages in practical applications.
1. Components and Functions of the Intelligent Control System
Core Control Module
The core control module of the double-sided labeling machine consists of a PLC (Programmable Logic Controller), which is responsible for executing commands and controlling the entire labeling process. The PLC collects sensor data and executes preset programs to ensure the machine completes labeling tasks with optimal path and speed. This module has strong computing and processing capabilities, allowing it to quickly respond to various production changes, maintaining efficient and stable labeling.
Human-Machine Interface (HMI)
The HMI serves as the bridge between the operator and the machine, usually presented in the form of a touchscreen. Through the HMI, operators can monitor the machine’s running status in real time, set labeling parameters, and troubleshoot issues. The intuitive interface design and multilingual support make it easy for operators to learn, even for beginners who can quickly become proficient.
High-Precision Sensor System
The machine is equipped with multiple high-precision sensors, including photoelectric sensors, position sensors, and pressure sensors. These sensors can monitor key data in real time during the labeling process, such as label position, labeling pressure, and speed. When abnormalities are detected, the system automatically adjusts the relevant parameters to ensure that each label is accurately applied to the product surface.
Automatic Detection and Feedback Mechanism
The automatic detection and feedback mechanism is a key part of the intelligent system of the double-sided labeling machine. Through closed-loop control, the machine can self-adjust based on feedback from the sensors. For example, when the sensors detect a misalignment in the label position, the system immediately adjusts the motion control module's parameters to correct the deviation. This self-correction capability significantly improves labeling accuracy and consistency.
2. Working Principle of the Intelligent Control System
The core of the intelligent control system is the closed-loop feedback mechanism. The system collects real-time data on the labeling process, such as feed speed and position deviations, through sensors and transmits this data to the PLC for analysis. Based on preset parameters and real-time data, the PLC issues adjustment commands to optimize the machine’s motion path and operating speed, ensuring that each label is precisely applied. This entire process is automated, eliminating the need for manual intervention and greatly enhancing production efficiency and product quality.
3. Advantages of the Intelligent Control System
Increased Production Efficiency
Traditional labeling equipment often requires manual adjustments of parameters and positions, which is inefficient and prone to errors. The intelligent control system of the double-sided labeling machine automatically adjusts and optimizes operations, reducing the need for human intervention, shortening downtime, and adjustment times, which in turn significantly boosts production efficiency.
Ensures Labeling Precision and Consistency
The intelligent control system continuously monitors and adjusts the labeling process, ensuring that each label is accurately applied to the designated position on the product. Even at high speeds, the machine maintains a labeling accuracy of ±0.1 mm. This level of precision and consistency is difficult to achieve through manual operations or ordinary mechanical equipment.
Reduced Manual Operations and Training Costs
Since the machine features automated adjustment functions, the operator's tasks are greatly simplified. They only need to input parameters and monitor the machine’s running status during the initial setup. The intuitive design of the HMI further reduces training time, enabling new employees to operate the machine proficiently after short-term training, thus lowering labor and training costs for the company.
Lower Defect Rates
In the labeling process, even minor deviations can cause labels to peel off or be misaligned, affecting the product's appearance and functionality. The intelligent control system of the double-sided labeling machine can detect and correct these deviations in real-time, ensuring that each product meets quality standards, effectively reducing defect rates.
4. Frequently Asked Questions (FAQ)
How to adjust the labeling accuracy of the double-sided labeling machine?
The labeling accuracy of the double-sided labeling machine can be adjusted through the parameter settings on the HMI. Operators can input the required labeling position and accuracy according to the product’s specific needs. The machine will automatically adjust the labeling path and pressure to achieve the best results. In addition, the automatic detection and feedback system continuously adjusts during operation to ensure high accuracy is maintained.
Does the intelligent control system require regular updates?
The intelligent control system does not require frequent updates, but regular software upgrades can help maintain the machine’s optimal performance. Manufacturers usually offer software update services to fix known issues and add new features. Users can either update the system themselves using the provided update package or contact technical support for assistance.
How to handle faults in the intelligent control system?
If the intelligent control system encounters a fault, the machine will display an error code and fault description on the HMI. Operators can troubleshoot the issue based on the fault information, such as checking sensor connections or restarting the machine. If the problem is more complex, it is advisable to contact professional technical support for repair.
Does the machine support remote monitoring and maintenance?
Yes, the double-sided labeling machine supports remote monitoring and maintenance. Through network connectivity, the machine’s operating status, parameter settings, and fault information can be viewed and adjusted via a remote monitoring system. This feature not only facilitates day-to-day management but also provides quick technical support when problems arise.
Conclusion
The intelligent control system of the double-sided labeling machine is crucial for enhancing equipment performance and production efficiency. Through the coordination of the core control module, HMI, and high-precision sensor system, the machine achieves full automation and high-precision control of the labeling process. For companies requiring high-efficiency and high-quality production, the intelligent control system of the double-sided labeling machine is an essential tool for improving production line automation and product quality.